Method for producing anisidine by mixed nitrochlorobenzene reacting in aqueous solvent
A technology of aminoanisole and nitrochlorobenzene, which is applied in chemical instruments and methods, preparation of organic compounds, and preparation of aminohydroxyl compounds, etc., which can solve the problems of increased difficulty in environmental protection, increased processing requirements, and increased production costs, etc. Problems, achieve the effect of reducing equipment investment, simplifying production process and reducing labor intensity
- Summary
- Abstract
- Description
- Claims
- Application Information
AI Technical Summary
Problems solved by technology
Method used
Image
Examples
Embodiment 1
[0018] (1) Etherification reaction: at 2M 3 Add 600kg of mixed nitrochlorobenzene (o-nitrochlorobenzene content 36.8%, p-nitrochlorobenzene content 61.6%, m-nitrochlorobenzene 1.6%) into the reaction kettle of 600kg, 120kg methanol, and 200kg sodium hydroxide. Heat to 70°C and add 700kg of water. It is heated to 120°C, the reaction pressure is controlled to 0.6 MPa, and the reaction time is maintained for 4 hours. Sampling and analysis showed that the total etherification conversion rate of o- and p-nitrochlorobenzene was 98.3%.
[0019] (2) Liquid-liquid separation: the reaction liquid in the previous step was cooled to room temperature (27°C), and the aqueous phase was separated to obtain 580 kg of etherified oil. After the impurities are filtered out of the water phase, it is recycled for secondary batching.
[0020] (3) Hydrogenation reduction: add 580kg of etherified oil obtained in the previous step, 1.5kg of Ce modified Pd-C catalyst, and 50kg of water to 1M 3 In the reacti...
Embodiment 2
[0025] (1) Etherification reaction: at 2M 3 Add mixed nitrochlorobenzene (o-nitrochlorobenzene content 44.7%, p-nitrochlorobenzene content 54.1%, m-nitrochlorobenzene 1.2%) 600kg, methanol 200kg, and sodium hydroxide 300kg into the reactor. Heat to 70°C and add 200kg of water. Heat to 80°C, control the reaction pressure to 0.2 MPa, and maintain the reaction time for 8 hours. Sampling and analysis showed that the total etherification conversion rate of o- and p-nitrochlorobenzene was 97.7%.
[0026] (2) Liquid-liquid separation: the reaction liquid in the previous step was cooled to room temperature (25°C), and the aqueous phase was separated to obtain 586 kg of etherified oil. After the impurities are filtered out of the water phase, it is recycled for secondary batching.
[0027] (3) Hydrogenation reduction: add 583kg of etherified oil obtained in the previous step, 2.0kg of La modified Pd-C catalyst, and 250kg of water to 1M 3 In the reactor, the reaction temperature is controll...
Embodiment 3
[0032] (1) Etherification reaction: at 2M 3 Add 600kg of mixed nitrochlorobenzene (65.7% of o-nitrochlorobenzene, 32.4% of p-nitrochlorobenzene, 1.9% of m-nitrochlorobenzene), 120kg of methanol, and 300kg of sodium hydroxide into the reactor. Heat to 70°C and add 500kg of water. Heat to 150°C, control the reaction pressure to 1.6 MPa, and maintain the reaction time for 4 hours. Sampling and analysis showed that the total etherification conversion rate of o- and p-nitrochlorobenzene was 99.4%.
[0033] (2) Liquid-liquid separation: the reaction liquid in the previous step was cooled to room temperature (24°C), and the aqueous phase was separated to obtain 586 kg of etherified oil. After the impurities are filtered out of the water phase, it is recycled for secondary batching.
[0034] (3) Hydrogenation reduction: add 586kg of etherified oil obtained in the previous step, 12kg of skeleton nickel catalyst, and 100kg of water to 1M 3 In the reactor, the reaction temperature is controll...
PUM
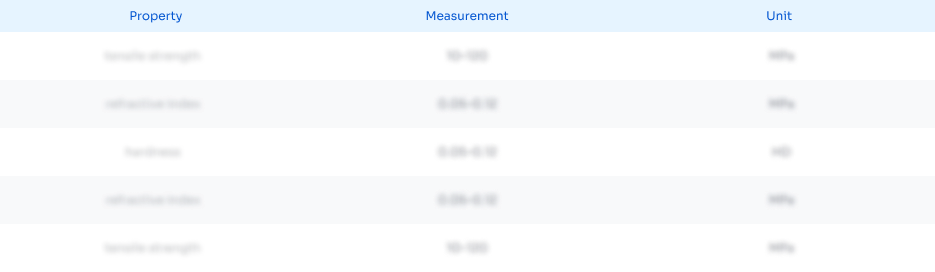
Abstract
Description
Claims
Application Information

- R&D Engineer
- R&D Manager
- IP Professional
- Industry Leading Data Capabilities
- Powerful AI technology
- Patent DNA Extraction
Browse by: Latest US Patents, China's latest patents, Technical Efficacy Thesaurus, Application Domain, Technology Topic, Popular Technical Reports.
© 2024 PatSnap. All rights reserved.Legal|Privacy policy|Modern Slavery Act Transparency Statement|Sitemap|About US| Contact US: help@patsnap.com