Five degree-of-freedom manipulator
A technology of robotic arms and degrees of freedom, applied in the field of robotic arms, can solve the problems of low mass and high stiffness, and achieve the effects of low mass, high stiffness, and easy assembly and maintenance.
- Summary
- Abstract
- Description
- Claims
- Application Information
AI Technical Summary
Problems solved by technology
Method used
Image
Examples
specific Embodiment approach 1
[0007] Specific implementation mode one: combine Figure 1 to Figure 9 Describe this embodiment, the mechanical arm described in this embodiment is constituted by a mechanical arm and a claw 1; Composed with the shoulder rotary joint 8; the disc drive servo motor 102 of the hand claw 1 is fixed in the spindle 201 of the wrist rotary joint 2 (fixed by screws), the claws are replaceable, and various claws can be replaced To facilitate clamping objects of different shapes, the wrist swivel joint connecting part 204 of the wrist swivel joint 2 is fixedly connected to the upper end of the auxiliary connecting plate 301 of the wrist joint 3, and the connecting end of the second connecting part 311 of the wrist joint 3 is connected to the small The upper end of the arm 4 is fixedly connected, the rear lower end of the small arm 4 is fixedly connected with the large gear of the elbow joint 5, the elbow joint bearing seat 512 in the elbow joint 5 is fixedly connected with the upper end...
specific Embodiment approach 2
[0008] Specific implementation mode two: combination figure 1 with Figure 5 To illustrate this embodiment, the wrist swivel joint 2 in this embodiment is composed of a mandrel 201, a wrist swivel joint servo motor 202, a wrist swivel joint housing 203, a wrist swivel joint connector 204 and two wrist swivel joint bearings 205; The lower end of the mandrel 201 is installed in the wrist revolving joint housing 203, and two wrist revolving joint bearings 205 are installed between the mandrel 201 and the wrist revolving joint housing 203, and the wrist revolving joint servo motor 202 is installed in the inner cavity of the mandrel 201 Among them, the output shaft of the wrist swivel joint servo motor 202 passes through the center hole of the lower end surface of the mandrel 201 and is fixedly connected to the central boss on the upper end of the wrist swivel joint connector 204, and the lower end of the wrist swivel joint housing 203 is connected to the wrist swivel joint The u...
specific Embodiment approach 3
[0009] Specific implementation mode three: combination figure 1 with Figure 4 Illustrate this embodiment, the claw 1 described in this embodiment is composed of, a disc drive servo motor 102, a rotating screw 103, a palm 104, a gear sleeve 105, two fingers 106, two parallel rods 107, two hands The claw seat 108 and two claws 109 are composed; the output shaft of the disc drive servo motor 102 is affixed to the input end of the rotating screw 103, and the output end of the rotating screw 103 passes through the center hole of the palm 104 and is arranged on the In the center of the palm of the palm 104, the gear sleeve 105 that is threadedly connected with it is housed on the screw lever of rotating leading screw 103, and the left side and the right side of rotating leading screw 103 are respectively provided with a finger 106 and a parallel rod 107, and described finger 106 A plurality of teeth are processed on the circular arc end surface of the lower end, and the gear slee...
PUM
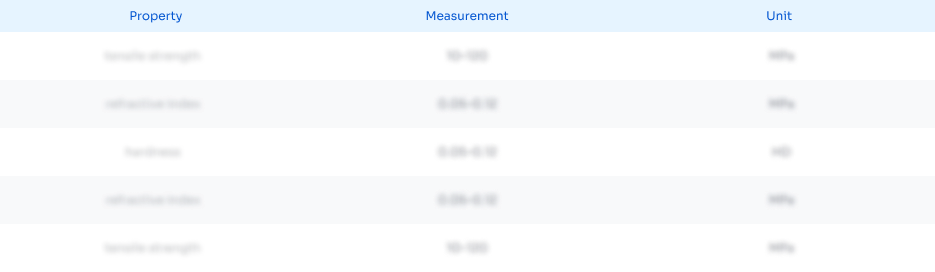
Abstract
Description
Claims
Application Information

- Generate Ideas
- Intellectual Property
- Life Sciences
- Materials
- Tech Scout
- Unparalleled Data Quality
- Higher Quality Content
- 60% Fewer Hallucinations
Browse by: Latest US Patents, China's latest patents, Technical Efficacy Thesaurus, Application Domain, Technology Topic, Popular Technical Reports.
© 2025 PatSnap. All rights reserved.Legal|Privacy policy|Modern Slavery Act Transparency Statement|Sitemap|About US| Contact US: help@patsnap.com