Clustered shunt type thermal protection for turbine rotor blade of aeroengine
A technology for aero-engines and turbine rotors, applied in the direction of engine components, machines/engines, blade support components, etc., can solve the problems of intermittent, uneven distribution of gas film holes, uneven gas film, etc.
- Summary
- Abstract
- Description
- Claims
- Application Information
AI Technical Summary
Problems solved by technology
Method used
Image
Examples
Embodiment Construction
[0012] Embodiments of the present invention will be further described below in conjunction with the accompanying drawings.
[0013] refer to figure 1 A plurality of cooling units H are arranged on the surface of the load-bearing skeleton 3 below the blade wall 2 of the turbine rotor blade 1 , and are distributed from the center of the turbine to the tail end of the turbine rotor blade 1 . The B-B section of the internal structure is expressed by A.
[0014] refer to figure 2 , the outer layer of the turbine rotor blade 1 is the blade wall surface 2, which is fixedly laid on the outside of the load-bearing framework 3, and the inner cavity N of the blade is formed inside, and the inner cavity spacer 4 is arranged in the inner layer. A number of air-introduction holes Y are provided around the load-bearing frame 3 to communicate with the inner cavity N of the blade, and a number of airflow channels T are opened on the outer layer of the load-bearing frame 3 .
[0015] refer ...
PUM
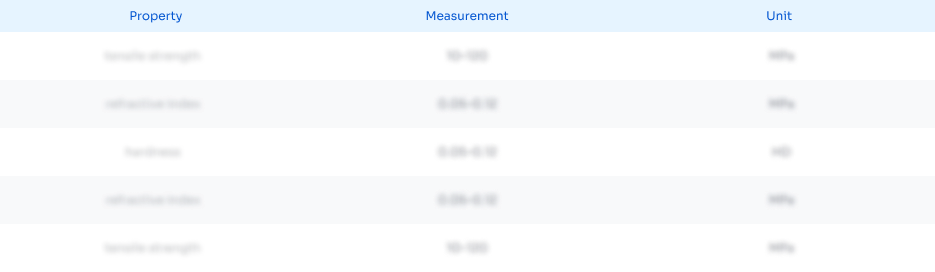
Abstract
Description
Claims
Application Information

- R&D
- Intellectual Property
- Life Sciences
- Materials
- Tech Scout
- Unparalleled Data Quality
- Higher Quality Content
- 60% Fewer Hallucinations
Browse by: Latest US Patents, China's latest patents, Technical Efficacy Thesaurus, Application Domain, Technology Topic, Popular Technical Reports.
© 2025 PatSnap. All rights reserved.Legal|Privacy policy|Modern Slavery Act Transparency Statement|Sitemap|About US| Contact US: help@patsnap.com