Three-chamber automatic clamping and locking mechanism
A locking mechanism and automatic technology, applied in the direction of clamping, metal processing mechanical parts, supports, etc., can solve the problems of poor clamping firmness, easy to loose, no self-locking function, etc., to achieve firm clamping of workpieces and flexible movements. Reliable, simple structure effect
- Summary
- Abstract
- Description
- Claims
- Application Information
AI Technical Summary
Problems solved by technology
Method used
Image
Examples
Embodiment Construction
[0010] Such as figure 1 , 2 Shown: 6 is the upper cover supported by the pillar 15. The upper cover 6 is inlaid with a clamping oil cylinder 7 connected to the hydraulic control device in the middle position, and a clamping piston 8 matched with the clamping oil cylinder 7 is sleeved in On the clamping piston rod 9, the lower end of the clamping piston rod 9 is connected with a pressure plate 13 through a pin 14. A dust cover 11 is screwed to the bottom end of the crimping cylinder 7.
[0011] The upper end of the clamping piston rod 9 extends to the inner cavity of the locking cylinder 16 which is located above the upper cover 6 and is perpendicular to the clamping cylinder 7. The locking piston 5 in the locking cylinder 16 is processed with an inclined surface 24 to match the inclined surface on the upper end of the clamping piston rod 9. The locking piston 5 is machined with a radial piston rod inlet hole 23 and an axial oil hole 31. The right cavity 29 passes through the oil...
PUM
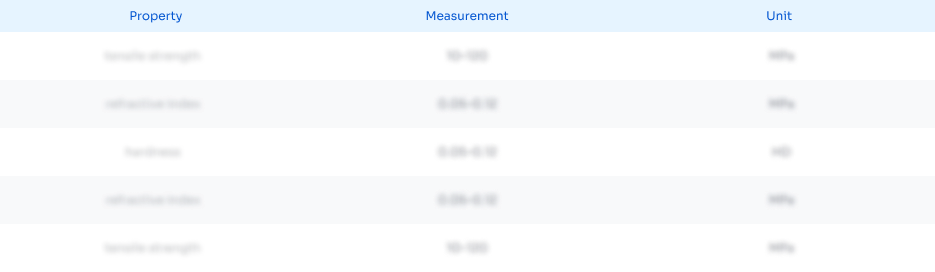
Abstract
Description
Claims
Application Information

- R&D Engineer
- R&D Manager
- IP Professional
- Industry Leading Data Capabilities
- Powerful AI technology
- Patent DNA Extraction
Browse by: Latest US Patents, China's latest patents, Technical Efficacy Thesaurus, Application Domain, Technology Topic, Popular Technical Reports.
© 2024 PatSnap. All rights reserved.Legal|Privacy policy|Modern Slavery Act Transparency Statement|Sitemap|About US| Contact US: help@patsnap.com