Apparatus and method for non-contacting blade oscillation measurement
A vibration measurement, non-contact technology, used in measurement devices, vibration measurement in solids, measurement of vibration and other directions, can solve problems such as interference and measurement data errors, and achieve the effect of improving amplitude resolution
- Summary
- Abstract
- Description
- Claims
- Application Information
AI Technical Summary
Problems solved by technology
Method used
Image
Examples
Embodiment Construction
[0029] figure 1 The schematic cross-sectional view shown shows the correction of the effective detector position by an integrated radial gap analysis according to the invention in non-contact blade vibration measurement (BSSM).
[0030] Here, four capacitive sensors 6 , 7 , 8 , 9 are arranged distributed on the circumference of the compressor housing 2 . The mounting of the sensors 6 , 7 , 8 , 9 takes place, for example, by screwing them into corresponding threaded holes on the outer shell of the housing.
[0031] In addition, in figure 1 The housing axis 4 and the rotor axis 5 in the center of the compressor housing 2 are also shown in . The two axes 4 , 5 are not aligned in the present embodiment, but are offset from each other. The circumference of the rotor 3 equipped with rotor blades is indicated by the circle drawn with dotted lines in the housing 2 .
[0032]Among them, the first sensor 6 is used to measure the gap d1 between the housing inner wall of the housing 2...
PUM
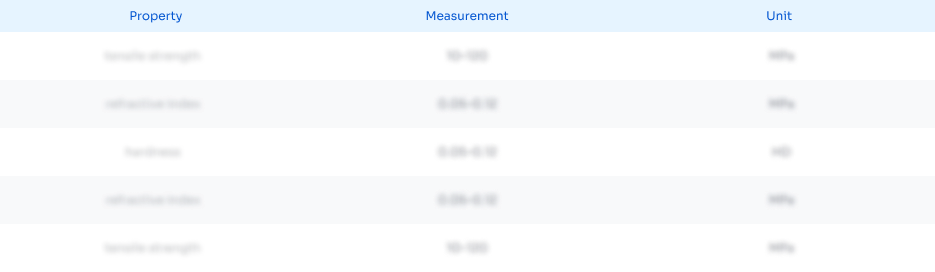
Abstract
Description
Claims
Application Information

- Generate Ideas
- Intellectual Property
- Life Sciences
- Materials
- Tech Scout
- Unparalleled Data Quality
- Higher Quality Content
- 60% Fewer Hallucinations
Browse by: Latest US Patents, China's latest patents, Technical Efficacy Thesaurus, Application Domain, Technology Topic, Popular Technical Reports.
© 2025 PatSnap. All rights reserved.Legal|Privacy policy|Modern Slavery Act Transparency Statement|Sitemap|About US| Contact US: help@patsnap.com