Periodic damping structure for automobile and absorption vibration denoise method thereof
A damping structure, vibration reduction and noise reduction technology, applied in the direction of spring/shock absorber, vibration suppression adjustment, mechanical equipment, etc., can solve the problems of cost increase, inconvenient processing, complex structure, etc., and achieve long service life and easy processing and molding , low-cost effect
- Summary
- Abstract
- Description
- Claims
- Application Information
AI Technical Summary
Problems solved by technology
Method used
Image
Examples
Embodiment 2
[0044] Example 2: Application of vehicle body roof vibration reduction
[0045] In this embodiment, the substrate to be damped is the roof of the vehicle body. Along the length direction of the ceiling, paste the damping sheet periodically and parallel on the roof of the vehicle body. Since the width B of the base plate is 94 cm, the width a of the damping sheet is 4.5 cm, and its length d should be equal to or slightly smaller than the width B of the base plate, which is 84 cm. The relative interval width ( Center distance of damping sheet) is 17.5cm.
[0046] The difference between this embodiment and Embodiment 1 is that the base plate 1 in Embodiment 1 is in a state of free suspension, while in this embodiment the roof is in a state of four sides being fixed. When the vehicle is running, the roof of the vehicle body vibrates due to engine vibration, road excitation, and air friction. After pasting the periodic damping structure, part of the vibration energy of the roof o...
Embodiment 3
[0047] Example 3: Application of vibration reduction on the rear seat floor of the vehicle body
[0048] In this embodiment, the substrate to be damped is the rear seat floor of the vehicle body. Along the length direction of the rear seat floor, the damping sheet 2 is periodically pasted on the rear seat floor in parallel. The difference between this embodiment and Embodiment 1 is that the shape of the rear seat floor of the vehicle body is irregular, restricted by the shape of the base plate 1, the length of the damping sheet 2 is different, and in order to facilitate its installation, a damping material is used between the damping sheets 2 The connection, the width a of the damping plate, the spacing distance, and the number of cycles must meet the requirements.
Embodiment 4
[0049] Example 4: Application of Vibration Damping on the Rear Floor of the Vehicle Body
[0050] Such as Figure 5 As shown, the damping substrate 1 in this embodiment is the rear floor of the vehicle body, and the damping sheet 2 is periodically pasted on the rear seat floor in parallel along the length direction of the rear floor. The difference between this embodiment and Embodiment 1 is that the rear floor area of the vehicle body is small, and only three cycles of the damping structure can be applied after meeting the size requirements of the damping sheet 2 .
PUM
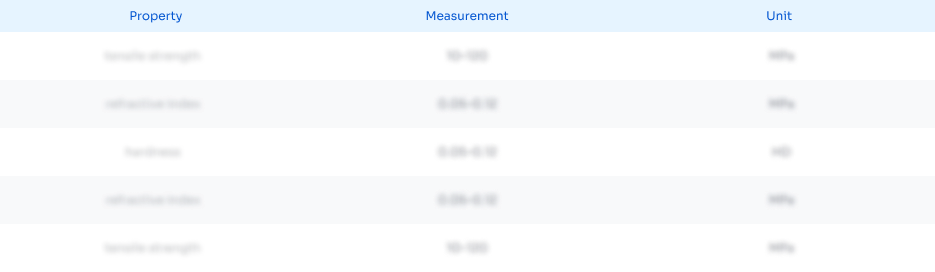
Abstract
Description
Claims
Application Information

- R&D
- Intellectual Property
- Life Sciences
- Materials
- Tech Scout
- Unparalleled Data Quality
- Higher Quality Content
- 60% Fewer Hallucinations
Browse by: Latest US Patents, China's latest patents, Technical Efficacy Thesaurus, Application Domain, Technology Topic, Popular Technical Reports.
© 2025 PatSnap. All rights reserved.Legal|Privacy policy|Modern Slavery Act Transparency Statement|Sitemap|About US| Contact US: help@patsnap.com