Roll rigidity controller of vehicle
A stiffness control, vehicle technology, applied in vehicle components, transportation and packaging, interconnection systems, etc., to solve problems such as insufficient consideration of lateral acceleration
- Summary
- Abstract
- Description
- Claims
- Application Information
AI Technical Summary
Problems solved by technology
Method used
Image
Examples
no. 1 example
[0082] figure 1 It is a schematic configuration diagram showing a first embodiment of a roll stiffness control device for a vehicle based on the present invention applied to a vehicle provided with active stabilizers on the front wheel side and the rear wheel side.
[0083] figure 1 Among them, 10FL and 10FR respectively represent the left and right front wheels of the vehicle 12 , and 10RL and 10RR respectively represent the left and right rear wheels of the vehicle 12 . Left and right front wheels 10FL and 10FR as steered wheels are steered via tie rods 14L and 14R by a power steering device 14 driven in response to steering of a steering wheel 14A by the driver. In addition, the drive form of the vehicle to which the roll stiffness control device of the present invention is applied may be any of front-wheel drive, rear-wheel drive, and four-wheel drive.
[0084] An active stabilizer 16 is provided between the left and right front wheels 10FL and 10FR, and an active stab...
no. 2 example
[0122] Figure 7 is a flowchart showing a lateral acceleration calculation routine of the second embodiment of the vehicle roll stiffness control device of the present invention. In addition, in Figure 7 in, with image 3 Steps shown are identical to those marked with image 3 The same step number as the one marked in .
[0123]In this second embodiment, the main routine of roll stiffness control except in step 200 follows Figure 7 The flow chart shown calculates the lateral accelerations Gyf and Gyr of the vehicle at the front wheel position and the rear wheel position, except that, as described above figure 2 The flowchart shown performs the same processing as that of the first embodiment described above. Additionally, if Figure 7 As shown, steps 210 to 220, 240, and 245 of the lateral acceleration calculation routine perform the same processing as that of the first embodiment described above.
[0124] When step 220 is completed, the steps corresponding to steps 2...
PUM
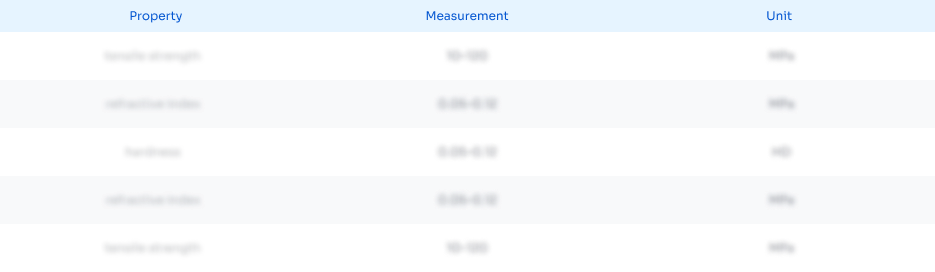
Abstract
Description
Claims
Application Information

- R&D
- Intellectual Property
- Life Sciences
- Materials
- Tech Scout
- Unparalleled Data Quality
- Higher Quality Content
- 60% Fewer Hallucinations
Browse by: Latest US Patents, China's latest patents, Technical Efficacy Thesaurus, Application Domain, Technology Topic, Popular Technical Reports.
© 2025 PatSnap. All rights reserved.Legal|Privacy policy|Modern Slavery Act Transparency Statement|Sitemap|About US| Contact US: help@patsnap.com