Large-strain electrostriction ceramic material and preparation method thereof
A ceramic material and stretching technology, which is applied in the field of large-strain electrostrictive ceramic materials and its preparation, can solve the development needs and strains of displacement actuators and large-energy electroacoustic transducers that are difficult to meet large strains Small problems, to achieve the effect of high electromechanical conversion efficiency, large mechanical thrust, wide operating temperature range
- Summary
- Abstract
- Description
- Claims
- Application Information
AI Technical Summary
Problems solved by technology
Method used
Image
Examples
Embodiment 1
[0020] As PbO: 43mol%, ZrO 2 : 35mol%, SnO 2 : 10mol%, TiO 2 : 5mol%, BaO: 5mol%, La 2 o 3 : 4mol% raw material ratio weighing. Deionized water is used as a medium, zirconia balls are used as grinding balls, and the weight ratio of raw materials, deionized water and zirconia balls is 0.8:1.0:3.0. The above raw materials were ball milled for 6 hours, and then dried at 120° C. for 24 hours. Through the ball milling process, the raw materials are ground into powders with an average particle size of less than 1 μm. Press the powder into a block, place it in an aluminum oxide crucible and seal it with a cover. The precursor with perovskite crystal phase was pre-fired at 850°C for 4 hours. Dry the calcined block after secondary ball milling. The powder after the secondary ball milling is made into a green body through granulation, compaction, plastic discharge and other processes. Place the biscuit in an aluminum oxide crucible, cover and seal it, and heat it in an electric...
Embodiment 2
[0023] As PbO: 44mol%, ZrO 2 : 25mol%, SnO 2 : 15mol%, TiO 2 : 10mol%, La 2 o 3 : 6mol%, BaO: 3mol% raw material ratio weighing. Chemically pure anhydrous ethanol is used as a medium, zirconia balls are used as grinding balls, and the weight ratio of raw materials, deionized water and zirconia balls is 0.6:1.2:3.0. The above raw materials were ball milled for 6 hours, and then dried at 60° C. for 12 hours. Through the ball milling process, the raw materials are ground into powders with an average particle size of less than 1 μm. Press the powder into a block, place it in an aluminum oxide crucible and seal it with a cover. The precursor with the perovskite crystal phase was pre-fired at 800°C for 6 hours. Dry the calcined block after secondary ball milling. The powder after the secondary ball milling is made into a green body through granulation, compaction, plastic discharge and other processes. Place the biscuit in an aluminum oxide crucible, cover and seal it, and ...
Embodiment 3
[0025] As PbO: 45mol%, ZrO 2 : 27mol%, SnO 2 : 13mol%, TiO 2 : 10mol%, La 2 o 3 : 8mol%, BaO: 1mol% raw material ratio weighing. Deionized water is used as a medium, zirconia balls are used as grinding balls, and the weight ratio of raw materials, deionized water and zirconia balls is 0.8:1.0:3. The above raw materials were ball milled for 5 hours, and then dried at 110° C. for 48 hours. Through the ball milling process, the raw materials are ground into powders with an average particle size of less than 1 μm. Press the powder into a block, place it in an aluminum oxide crucible and seal it with a cover. The precursor with the perovskite crystal phase was pre-fired at 900°C for 3 hours. Dry the calcined block after secondary ball milling. The powder after the secondary ball milling is made into a green body through granulation, compaction, plastic discharge and other processes. Place the biscuit in an aluminum oxide crucible, cover and seal it, and heat it in an elect...
PUM
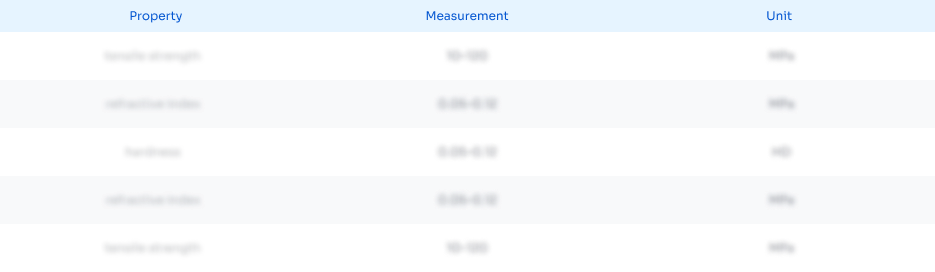
Abstract
Description
Claims
Application Information

- R&D
- Intellectual Property
- Life Sciences
- Materials
- Tech Scout
- Unparalleled Data Quality
- Higher Quality Content
- 60% Fewer Hallucinations
Browse by: Latest US Patents, China's latest patents, Technical Efficacy Thesaurus, Application Domain, Technology Topic, Popular Technical Reports.
© 2025 PatSnap. All rights reserved.Legal|Privacy policy|Modern Slavery Act Transparency Statement|Sitemap|About US| Contact US: help@patsnap.com