Turbine heat shield assembly
A technology of heat shield and turbine impeller, which is applied to engine components, gas turbine devices, mechanical equipment, etc., can solve problems such as leakage, high cost, oil leakage, etc., and achieve the effect of contributing to manufacturing, maintaining efficiency, and being cost-effective.
- Summary
- Abstract
- Description
- Claims
- Application Information
AI Technical Summary
Problems solved by technology
Method used
Image
Examples
Embodiment Construction
[0023] see image 3 and Figure 4 , a part of a turbocharger with a bearing housing 100 is shown in these figures. Bearing housing 100 defines a circumferential channel or recess 150 at one end near the periphery of the bearing housing. As will be explained in more detail below, channel 150 is used to position and connect a heat shield 200 to bearing housing 100 .
[0024] Preferably the channel 150 is concentrically aligned with a turbine wheel or rotor 250 . The heat shield 200 has a central hole 210 therethrough. Preferably the central bore 210 is concentrically aligned with the turbine wheel 250 and allows a shaft 220 to pass therethrough. Shaft 220 is attached at one end opposite a compressor wheel (not shown).
[0025] Heat shield 200 provides thermal protection for various components of the turbocharger, including lubrication system 230 . Various other components may be used with the turbocharger of the exemplary embodiment, but are not described. These other com...
PUM
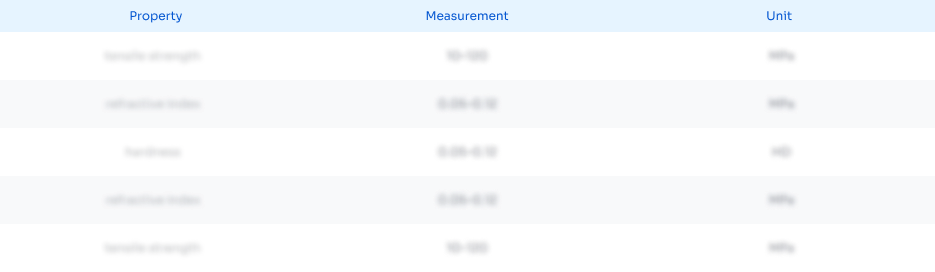
Abstract
Description
Claims
Application Information

- R&D
- Intellectual Property
- Life Sciences
- Materials
- Tech Scout
- Unparalleled Data Quality
- Higher Quality Content
- 60% Fewer Hallucinations
Browse by: Latest US Patents, China's latest patents, Technical Efficacy Thesaurus, Application Domain, Technology Topic, Popular Technical Reports.
© 2025 PatSnap. All rights reserved.Legal|Privacy policy|Modern Slavery Act Transparency Statement|Sitemap|About US| Contact US: help@patsnap.com