High-torsion plate welding screw cap
A flat plate welding, high torsion technology, applied in the direction of nuts, connecting components, threaded fasteners, etc., can solve the problem that the bolts cannot be locked tightly, and achieve the effect of not being easy to face and improving the torsional strength
- Summary
- Abstract
- Description
- Claims
- Application Information
AI Technical Summary
Problems solved by technology
Method used
Image
Examples
Embodiment Construction
[0011] Below in conjunction with accompanying drawing and embodiment the present invention is described in detail:
[0012] Such as Figure 3-5 As shown, the embodiment of the high-torque flat welding nut of the present invention includes a welding plate body 3 and a nut body 4 fixedly mounted on the welding plate body 3 .
[0013] The welding plate body 3 has a circular installation hole 30 penetrating through its top and bottom surfaces, and three welding protrusions 31 protruding from its bottom surface at intervals and symmetrically. The mounting hole 30 has a large aperture portion 301 , a shoulder portion 302 , and a small aperture portion 303 with a smaller diameter than the large aperture portion 301 from bottom to top.
[0014] The nut body 4 includes a nut portion 41 with thread 410 inside, an annular upper clamping portion 42 protruding radially from the bottom edge of the outer peripheral surface of the nut portion 41 , and a The annular lower clamping portion 43...
PUM
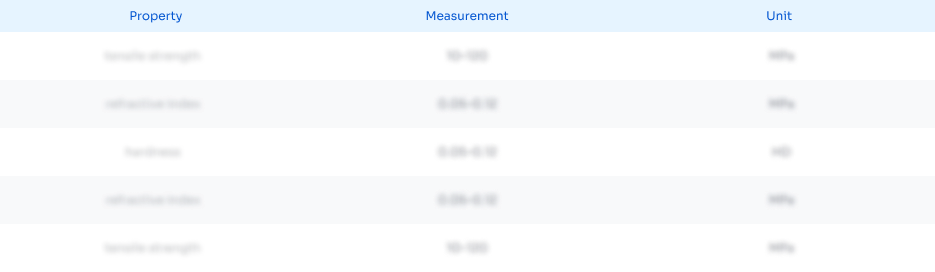
Abstract
Description
Claims
Application Information

- R&D
- Intellectual Property
- Life Sciences
- Materials
- Tech Scout
- Unparalleled Data Quality
- Higher Quality Content
- 60% Fewer Hallucinations
Browse by: Latest US Patents, China's latest patents, Technical Efficacy Thesaurus, Application Domain, Technology Topic, Popular Technical Reports.
© 2025 PatSnap. All rights reserved.Legal|Privacy policy|Modern Slavery Act Transparency Statement|Sitemap|About US| Contact US: help@patsnap.com