Supersonic inspection method for profiled bar overwelded hole welding joint
A through-hole and ultrasonic technology, which is applied to the analysis of solids using sonic/ultrasonic/infrasonic waves, can solve the problems of small through-hole space, difficulty in receiving reflected echoes, and inability to ensure the quality of welds, reducing construction steps. , save time and raw materials, improve the effect of weld quality
- Summary
- Abstract
- Description
- Claims
- Application Information
AI Technical Summary
Problems solved by technology
Method used
Image
Examples
Embodiment Construction
[0062] Below in conjunction with the accompanying drawings and specific implementation methods, the ultrasonic flaw detection method of the welded seam at the section steel passing through the welding hole of the present invention will be further described in detail:
[0063] The section steel in the method for ultrasonic flaw detection of the weld seam where the section steel passes through the welding hole of the present invention refers to the I-beam 4 .
[0064] Such as Figure 4 As shown, the ultrasonic flaw detection method at 2 places of the section steel welding hole of the present invention comprises the following steps:
[0065] 1. Backing plate welding step S1: Weld the deck 3 with a steel plate, mark the position where the I-beam 4 should be set on the deck 3, cut the I-beam 4 and set the welding hole 2, and use the deck 3 as a backing plate, For pad welding,
[0066] 2. Clean and polish flaw detection surface S2,
[0067] 3. Grinding the inner weld of the weldi...
PUM
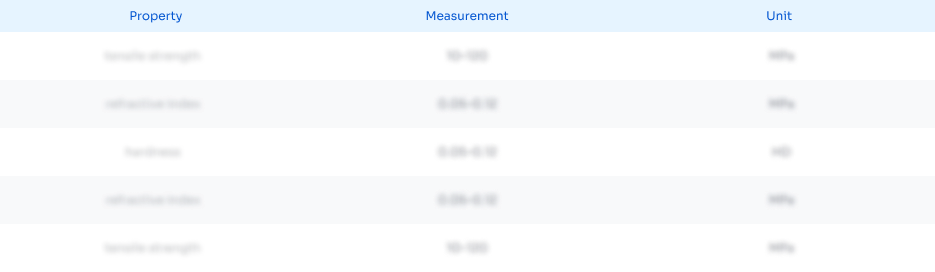
Abstract
Description
Claims
Application Information

- R&D
- Intellectual Property
- Life Sciences
- Materials
- Tech Scout
- Unparalleled Data Quality
- Higher Quality Content
- 60% Fewer Hallucinations
Browse by: Latest US Patents, China's latest patents, Technical Efficacy Thesaurus, Application Domain, Technology Topic, Popular Technical Reports.
© 2025 PatSnap. All rights reserved.Legal|Privacy policy|Modern Slavery Act Transparency Statement|Sitemap|About US| Contact US: help@patsnap.com