Foundry technique method of lower support board of ball type support
A spherical bearing and casting process technology, applied in the direction of manufacturing tools, casting molding equipment, casting molds, etc., can solve the problems of large number of risers, easy occurrence of trachoma, sand inclusion, unqualified ultrasonic flaw detection inspection, etc. The method is simple and easy, improves the speed of process preparation, and changes the effect of adverse effects
- Summary
- Abstract
- Description
- Claims
- Application Information
AI Technical Summary
Problems solved by technology
Method used
Image
Examples
Embodiment approach 1
[0025] As shown in Figures 1 and 2: a casting process for the lower bearing plate of a spherical bearing is based on the shape and structure of the lower bearing plate of the spherical bearing, a square plate-shaped piece, one side is a large plane, and the other side has an edge The four corners are in the shape of a flat plate, and the middle part is a circular boss with a concave spherical surface. The large plane faces upward and is poured horizontally. A cylindrical riser is set in the center of the large plane, and a horizontal subsidy is set around the riser. To meet the feeding requirements of sequential solidification of castings. Molten steel pouring adopts two straight sprues to pour at the same time, and four inner runners are located at the edge of the riser and are introduced into the mold through the bottom trans tangent.
[0026] Its technological implementation process is as follows:
[0027] 1. Make a sand mold according to the structural shape of the lower ...
Embodiment approach 2
[0035] As shown in Figures 1, 3, and 4: the casting process of the lower bearing plate of this kind of spherical bearing can also be used for steel castings whose lower bearing plate is a rectangular boss structure shape, and the lower bearing plate is large. The plane faces upward and pours horizontally; the bottom surface of the rectangular convex platform and the concave spherical surface in the middle of the mold on the other side are scraped off with the scraper 1, and the rest of the parts are pounded out of the real sample model. Other processes are the same as the above-mentioned circular boss casting casting process.
[0036] The casting process for the lower bearing plate of the spherical bearing can also be used for other steel castings with similar structural shapes.
PUM
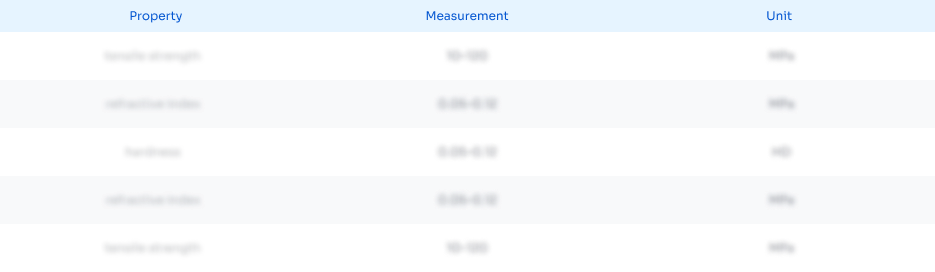
Abstract
Description
Claims
Application Information

- R&D Engineer
- R&D Manager
- IP Professional
- Industry Leading Data Capabilities
- Powerful AI technology
- Patent DNA Extraction
Browse by: Latest US Patents, China's latest patents, Technical Efficacy Thesaurus, Application Domain, Technology Topic, Popular Technical Reports.
© 2024 PatSnap. All rights reserved.Legal|Privacy policy|Modern Slavery Act Transparency Statement|Sitemap|About US| Contact US: help@patsnap.com