Motor transmission system without bearing for multiphase single sleeve winding
A bearingless motor and transmission system technology, applied in the control system, AC motor control, electrical components, etc., can solve the problems of voltage equalization, current equalization difficulties, low reliability, and reduced reliability, etc., to achieve fault-tolerant operation and structure Simple, Highly Reliable Effects
- Summary
- Abstract
- Description
- Claims
- Application Information
AI Technical Summary
Problems solved by technology
Method used
Image
Examples
Embodiment Construction
[0019] Further illustrate the present invention below in conjunction with accompanying drawing:
[0020] refer to figure 1 , the multi-phase single-set winding bearingless motor transmission system of the present invention comprises:
[0021] A multi-phase AC motor 1 has a set of windings with n≥5 phases, the stator windings of the motor are composed of n windings whose axes are successively separated by an angle of 2π / n, and each phase winding contains both odd and even space harmonics;
[0022] The polyphase inverter 2 is used to supply power to the polyphase AC motor 1. The number of phases of the polyphase inverter 2 is equal to the phase number n of the polyphase AC motor 1. When the single-ended power supply is used, one end of each phase winding of the motor is Star connection, the input end of each phase winding is connected to the output end of each phase bridge arm of the inverter; when double-ended power supply is used, the two ends of each phase winding of the mot...
PUM
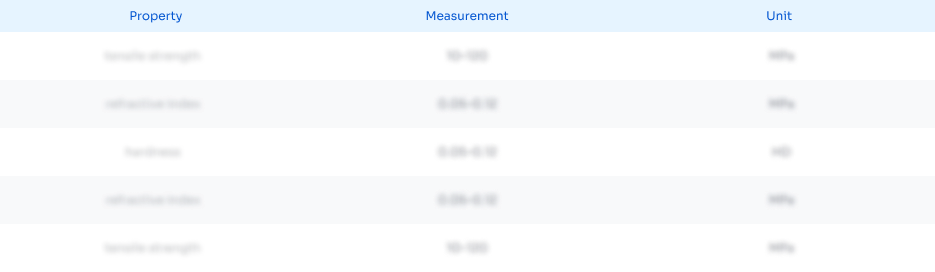
Abstract
Description
Claims
Application Information

- R&D
- Intellectual Property
- Life Sciences
- Materials
- Tech Scout
- Unparalleled Data Quality
- Higher Quality Content
- 60% Fewer Hallucinations
Browse by: Latest US Patents, China's latest patents, Technical Efficacy Thesaurus, Application Domain, Technology Topic, Popular Technical Reports.
© 2025 PatSnap. All rights reserved.Legal|Privacy policy|Modern Slavery Act Transparency Statement|Sitemap|About US| Contact US: help@patsnap.com