Casting method and device for ingot metal
A casting method and technology for metal ingots, which are applied in the field of casting methods and devices for metal ingots, can solve problems such as water accumulation in metal ingots, explosions, and inability to transfer volume compensation, and achieve the effect of eliminating internal shrinkage cavities and eliminating influencing factors
- Summary
- Abstract
- Description
- Claims
- Application Information
AI Technical Summary
Problems solved by technology
Method used
Image
Examples
Embodiment 1
[0028] A method for casting metal ingots, which is used to produce zinc-based alloy ingots. It uses an open mold for casting. It first casts molten zinc-based alloy liquid into the ingot mold, and then casts the zinc-based alloy ingot in the solidification process. The upper surface is heated and kept warm so that the cooling rate of this surface is lower than that of the other surfaces of the ingot, and the heating is not stopped until the volume of the molten metal in the center of the zinc-based alloy ingot during the cold shrinkage process is fully compensated by the molten metal on the surface .
[0029] A casting apparatus for metal ingots, such as figure 1 , figure 2 , shown in Fig. 5, it is used for producing the zinc base alloy ingot 6 that is 1000Kg, adopts mold 1 casting, and the cross section of mold 1 length direction is the cuboid open container of T-type that is wide at the top and narrow at the bottom, and heat preservation cover 5 is to set There is a conca...
Embodiment 2
[0032] A method for casting metal ingots, which is used to produce zinc-based alloy ingots. It uses an open mold for casting. It first casts molten zinc-based alloy liquid into the ingot mold, and then casts the zinc-based alloy ingot in the solidification process. The upper surface is heated and kept warm so that the cooling rate of this surface is lower than that of the other surfaces of the ingot, and the heating is not stopped until the volume of the molten metal in the center of the zinc-based alloy ingot during the cold shrinkage process is fully compensated by the molten metal on the surface .
[0033] A casting apparatus for metal ingots, such as figure 1 , figure 2 , shown in Fig. 5, it is used for producing the zinc base alloy ingot 6 of 1700Kg, adopts mold 1 to cast, and the cross section of mold 1 length direction is the rectangular parallelepiped container of upper wide and lower narrow T-shaped, and insulation cover 5 is set There is a concave inner cavity wit...
Embodiment 3
[0036] A method for casting metal ingots, which is used to produce zinc ingots. It adopts open mold casting. It first pours molten zinc liquid into the ingot mold, and then heats and insulates the upper surface of the zinc ingot in the solidification process. The cooling rate of this surface is lower than that of the other surfaces of the ingot, and the heating is not stopped until the volume of the molten metal in the center of the zinc ingot during the cold shrinkage process is fully compensated by the molten metal on the surface.
[0037] A casting apparatus for metal ingots, such as figure 1 , image 3 , shown in Fig. 5, it is used for producing the zinc ingot that specification is 1000Kg, adopts mold 1 casting, and the cross section of mold 1 lengthwise direction is the cuboid open container of T-shaped of upper wide and lower narrow, and insulation cover 5 is to be provided with heating device The inner cavity of the inner cavity, the cover that is docked with the edge ...
PUM
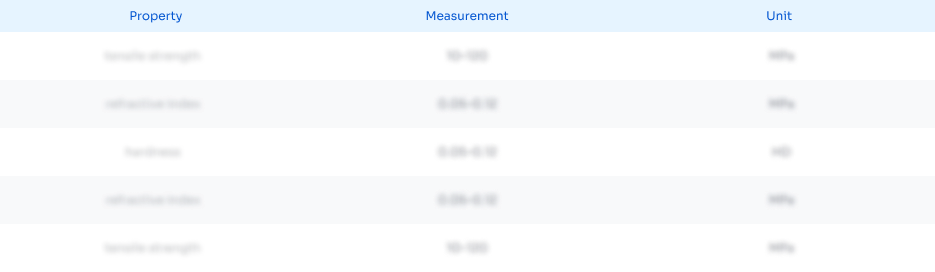
Abstract
Description
Claims
Application Information

- R&D
- Intellectual Property
- Life Sciences
- Materials
- Tech Scout
- Unparalleled Data Quality
- Higher Quality Content
- 60% Fewer Hallucinations
Browse by: Latest US Patents, China's latest patents, Technical Efficacy Thesaurus, Application Domain, Technology Topic, Popular Technical Reports.
© 2025 PatSnap. All rights reserved.Legal|Privacy policy|Modern Slavery Act Transparency Statement|Sitemap|About US| Contact US: help@patsnap.com