Flexible core of flexible tube terminal mould
A flexible and core head technology, applied in the field of flexible core heads, can solve the problems of wrinkling at the bending part, difficulty in bending thin-walled and small bending radius pipe fittings, and poor ovality of the bent pipe fittings.
- Summary
- Abstract
- Description
- Claims
- Application Information
AI Technical Summary
Problems solved by technology
Method used
Image
Examples
Embodiment Construction
[0013] The flexible core of the flexible pipe end mold shown in Figure 1-4 includes a straight core 1 and a universal spherical core 3, the straight core 1 is connected with the universal spherical core 3 through four pressure plates 9, and the straight core 1 A groove 10 adapted to the ball core head 5 of the universal ball core head 3 is provided at the tail of the ball head. The universal ball core head 3 is composed of a ball core head 5, 6 intermediate inner connectors 6, an intermediate outer ring 7 and 6 lower connectors 8, and the structure of the universal ball core head 3 is the ball core head 5 The middle inner connecting body 6 and the lower connecting body 8 are covered by the screw rod at the lower end, and the outer end surface of the middle inner connecting body 6 is covered with the middle outer ring 7; the structure of the ball core head 5 is: the ball core head 5 is a "person" The upper part is a spherical joint, the middle is provided with an inward card sl...
PUM
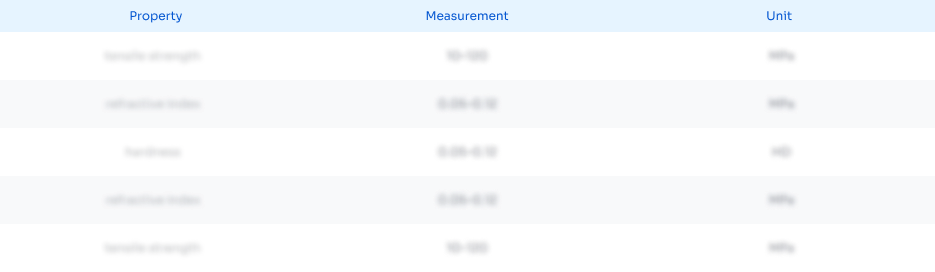
Abstract
Description
Claims
Application Information

- R&D
- Intellectual Property
- Life Sciences
- Materials
- Tech Scout
- Unparalleled Data Quality
- Higher Quality Content
- 60% Fewer Hallucinations
Browse by: Latest US Patents, China's latest patents, Technical Efficacy Thesaurus, Application Domain, Technology Topic, Popular Technical Reports.
© 2025 PatSnap. All rights reserved.Legal|Privacy policy|Modern Slavery Act Transparency Statement|Sitemap|About US| Contact US: help@patsnap.com