Method and apparatus for single-stage mixing cryogen refrigerating cycle liquefied natural gas
A technology of liquefied natural gas and mixed refrigerant, applied in refrigeration and liquefaction, liquefaction, gas fuel and other directions, can solve the problems of increased production cost, increased input cost, increased number of equipment, etc., to reduce equipment investment, reduce production costs, The effect of simplifying the looping process and operational control
- Summary
- Abstract
- Description
- Claims
- Application Information
AI Technical Summary
Problems solved by technology
Method used
Image
Examples
Embodiment 1
[0032] The schematic diagram of the device (without heavy hydrocarbon separation module) used in this embodiment mainly includes a refrigeration cycle system and a natural gas liquefaction system. The refrigeration cycle system consists of a compressor 32, a cooler 33, and a cold box (wherein the main equipment is Heat exchanger 31), mixed refrigerant throttle valve 34 (located in the cold box), etc. are connected by pipelines to form a closed refrigeration cycle system; the heat exchanger 31 in the cold box also passes through the natural gas throttle valve 35, etc. The natural gas inlet and outlet pipelines are connected into a natural gas liquefaction system; the position of the cooler 33 is on the top of the cold box (outside the cold box).
[0033] The mixed refrigerant used is composed of 5% N 2 , 35%CH 4 , 26% C 2 h 4 , 16% C 3 h 8 , 18% C 5 h 12 composition.
[0034] The method for liquefied natural gas in the single-stage mixed refrigerant refrigeration cycle ...
Embodiment 2
[0041] The schematic diagram of the device (having a heavy hydrocarbon separation module) used in this embodiment mainly includes a refrigeration cycle system and a natural gas liquefaction system. The refrigeration cycle system consists of a compressor 32, a cooler 33, and a cold box (where the main equipment is a Heater, including pre-cooling heat exchanger 311 and main cooling heat exchanger 312), mixed refrigerant throttle valve 34 (located in the cold box), etc. are connected by pipelines to form a closed refrigeration cycle system; the pre-cooling system in the cold box Cold heat exchanger 311 and main cold heat exchanger 312 are also connected with heavy hydrocarbon separator 36 and natural gas throttle valve 35 through natural gas inlet and outlet pipelines to form a natural gas liquefaction system.
[0042] The mixed refrigerant used is composed of 5% N 2 , 35%CH 4 , 26% C 2 h 4 , 16% C 3 h 8 , 18% C 5 h 12 composition.
[0043] The method for liquefied natura...
Embodiment 3
[0050] The schematic diagram of the device (without heavy hydrocarbon separation module) used in this embodiment mainly includes a refrigeration cycle system and a natural gas liquefaction system. The refrigeration cycle system consists of a compressor 32, a cooler 33, and a cold box (wherein the main equipment is Heat exchanger 31), mixed refrigerant throttle valve 34 (located in the cold box), etc. are connected by pipelines to form a closed refrigeration cycle system; the heat exchanger 31 in the cold box also passes through the natural gas throttle valve 35 The natural gas inlet and outlet pipelines are connected to form a natural gas liquefaction system; among them, the pipelines for natural gas entering and leaving the cold box are connected from the bottom to the top, and the pipelines for the mixed refrigerant to enter and exit the cold box are connected to the cold box in a bottom-to-bottom way.
[0051] The mixed refrigerant used is composed of 8% N 2 , 30%CH 4 , 28...
PUM
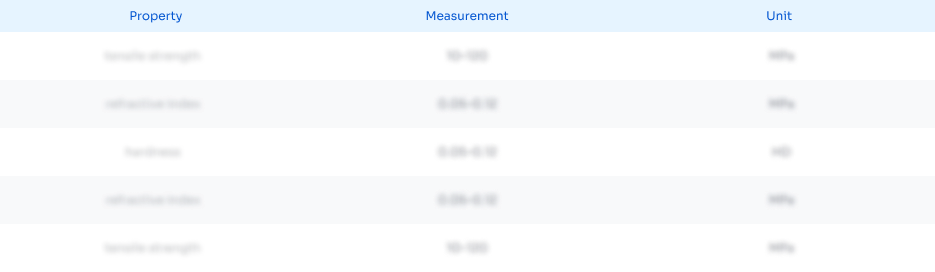
Abstract
Description
Claims
Application Information

- R&D Engineer
- R&D Manager
- IP Professional
- Industry Leading Data Capabilities
- Powerful AI technology
- Patent DNA Extraction
Browse by: Latest US Patents, China's latest patents, Technical Efficacy Thesaurus, Application Domain, Technology Topic, Popular Technical Reports.
© 2024 PatSnap. All rights reserved.Legal|Privacy policy|Modern Slavery Act Transparency Statement|Sitemap|About US| Contact US: help@patsnap.com