Direct drive type oil servo motor based on direct drive type electrohydraulic servo power source
An electro-hydraulic servo, direct-drive technology, applied in engine components, machines/engines, mechanical equipment, etc., can solve the problems of low efficiency and high failure rate, avoid overflow loss, improve reliability, and reduce the probability of failure Effect
- Summary
- Abstract
- Description
- Claims
- Application Information
AI Technical Summary
Problems solved by technology
Method used
Image
Examples
specific Embodiment approach 1
[0009] Specific implementation mode one: combine figure 2 and image 3 Describe this embodiment. This embodiment is composed of a servo amplifier 1, a direct-drive electro-hydraulic servo power source 2, a hydraulic cylinder 3 and a displacement sensor 4; the digital electro-hydraulic control system inputs the set oil motor stroke signal into the oil motor Servo amplifier 1 and displacement sensor 4 measure the feedback signal of the real-time displacement of hydraulic cylinder 3 to servo amplifier 1. Servo amplifier 1 compares and amplifies the two signals and outputs them to direct-drive electro-hydraulic servo power source 2. The hydraulic servo power source 2 drives the hydraulic cylinder 3 to move after receiving the electric control signal from the servo amplifier 1, and controls the opening and closing of the steam turbine valve and the opening degree of the valve. When the error between the position signal of the hydraulic cylinder 3 fed back by the position sensor 4...
specific Embodiment approach 2
[0010] Specific implementation mode two: combination image 3 This embodiment is described. The difference between this embodiment and the first embodiment is that two sets of direct-drive electro-hydraulic servo power sources 2 are used to connect to the hydraulic cylinder 3 . Two sets of direct-drive electro-hydraulic servo power source 2 are connected in parallel at the inlet and outlet of hydraulic cylinder 3 to realize redundant configuration; when the steam turbine valve is opened and the opening is adjusted, a set of direct-drive electro-hydraulic servo power source 2 is used to work, When the air valve is closed, two sets of direct-drive electro-hydraulic servo power sources 2 work simultaneously to speed up the closing speed of the air valve. When one set of direct-drive electro-hydraulic servo power source 2 fails, the system automatically switches to the second set of direct-drive electro-hydraulic servo power source 2 to ensure the normal operation of the oil motor...
specific Embodiment approach 3
[0011] Specific implementation mode three: combination image 3 This embodiment is described. The difference between this embodiment and specific embodiment 1 is that the replenishment valve 24 is composed of two hydraulic control check valves, and the two hydraulic control check valves are respectively the first hydraulic control check valve and the second hydraulic control check valve. control check valve; one oil port and the control oil port of the first hydraulic control check valve are respectively connected with the two oil passages between the two-way quantitative pump 23 and the hydraulic cylinder 3, and one oil port of the second hydraulic control check valve The connection mode of the control oil port is opposite to the connection mode between one oil port and the control oil port of the first hydraulic control check valve, and the other oil port of the first hydraulic control check valve is connected to the other port of the second hydraulic control check valve. Th...
PUM
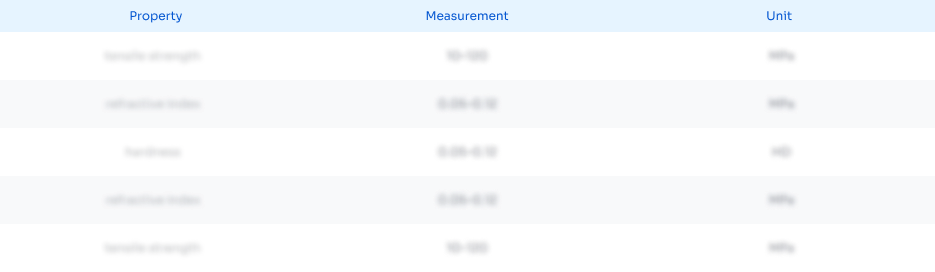
Abstract
Description
Claims
Application Information

- R&D Engineer
- R&D Manager
- IP Professional
- Industry Leading Data Capabilities
- Powerful AI technology
- Patent DNA Extraction
Browse by: Latest US Patents, China's latest patents, Technical Efficacy Thesaurus, Application Domain, Technology Topic, Popular Technical Reports.
© 2024 PatSnap. All rights reserved.Legal|Privacy policy|Modern Slavery Act Transparency Statement|Sitemap|About US| Contact US: help@patsnap.com