Control method of large-sized mining grinding mill end flange welding deformation
A control method and flange welding technology, applied in welding equipment, welding equipment, auxiliary welding equipment, etc., can solve the problem of increasing the lateral shrinkage force of the outer weld metal, the flange hook at the end of the welding sequence is incorrect, and the welder's non-existence. Correct welding and other issues can shorten the production cycle, reduce production costs, and reduce welding deformation.
- Summary
- Abstract
- Description
- Claims
- Application Information
AI Technical Summary
Problems solved by technology
Method used
Image
Examples
Embodiment Construction
[0037] Take φ8.8×4.8m semi-autogenous mill end flange welding as an example. The technical parameters of the mill are: outer dimension φ9300×4800mm, end flange outer diameter 9300mm, inner diameter 8800mm, cylinder thickness 60mm, material Q235D.
[0038] Groove butt joint method is handled according to the equation of internal and external equality, relevant parameters see Figure 7 , the specific control method is as follows:
[0039] 1. Use the welding rod J502 φ5 welding rod for spot welding at intervals of 500mm between the cylinder body and the end flange. The spot welding length is about 30mm. And the connecting plate is used to connect the cylinder section and the end flange on the inner side of the cylinder body.
[0040] 2. Hang the cylinder on the welding roller, heat the connection between the cylinder and the end flange to 100-150°C with gas, select HO8A, Φ4mm welding wire, use the manipulator to use submerged arc welding, and use multiple welding methods during...
PUM
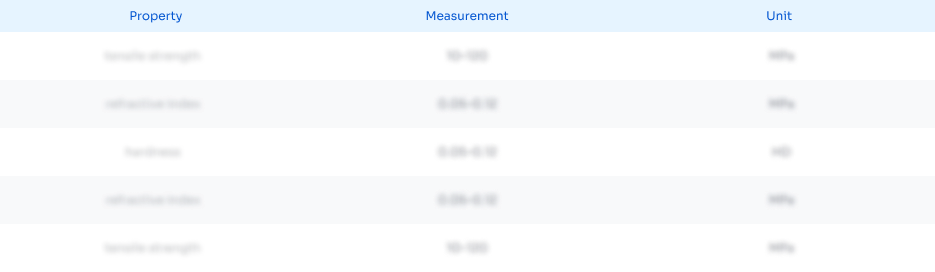
Abstract
Description
Claims
Application Information

- R&D
- Intellectual Property
- Life Sciences
- Materials
- Tech Scout
- Unparalleled Data Quality
- Higher Quality Content
- 60% Fewer Hallucinations
Browse by: Latest US Patents, China's latest patents, Technical Efficacy Thesaurus, Application Domain, Technology Topic, Popular Technical Reports.
© 2025 PatSnap. All rights reserved.Legal|Privacy policy|Modern Slavery Act Transparency Statement|Sitemap|About US| Contact US: help@patsnap.com