Last type leather welt sandals turning-outwards shoes, manufacture method thereof and special last pushing seat
A welt and turn-out technology, which is applied in shoe lasts, footwear, soles, etc., can solve the problem of unstable toe port or head reinforcement exposure, uneven or broken toe caps, and warped toe caps Problems such as difficulty in controlling the degree of difficulty, to achieve the effect of beautiful appearance, consistent warping of the toe, and reduction of material costs
- Summary
- Abstract
- Description
- Claims
- Application Information
AI Technical Summary
Problems solved by technology
Method used
Image
Examples
Embodiment Construction
[0040] A kind of lasted leather welt-turned shoes, which includes a vamp 1 with the toe of the vamp already shaped, the lower end edge of the vamp 1 is turned to form a turn-out edge 2, and the width of the turn-out edge 2 is It is about 10 millimeters, and the bottom surface of valgus 2 is combined with leather midsole 3 with thread car, and the bottom surface of leather midsole 3 is pasted with outsole 5. The leather midsole 3 includes a midsole 6, and the edge of the midsole 6 is fixedly pasted with a leather welt 7 that can be combined with the outer cuff 2 of the shoe upper. Because the leather midsole 3 adopts the structure that the midsole 6 and the leather welt 7 are combined to form a combined leather midsole, the area of the midsole 6 is smaller than the area of the leather midsole of the previous Panbang practice, and the midsole 6 can be It is made of common materials, which greatly reduces the manufacturing cost and makes the whole shoe lighter and softer.
...
PUM
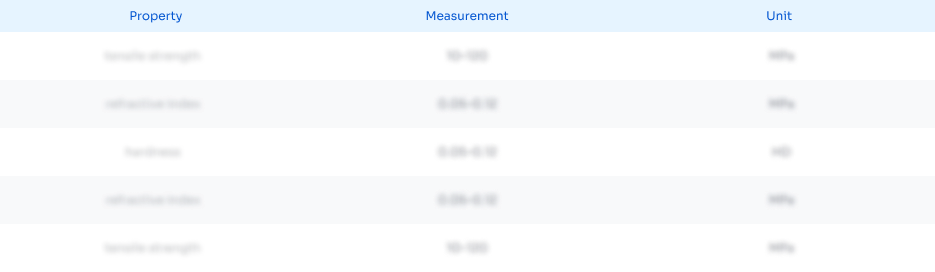
Abstract
Description
Claims
Application Information

- R&D
- Intellectual Property
- Life Sciences
- Materials
- Tech Scout
- Unparalleled Data Quality
- Higher Quality Content
- 60% Fewer Hallucinations
Browse by: Latest US Patents, China's latest patents, Technical Efficacy Thesaurus, Application Domain, Technology Topic, Popular Technical Reports.
© 2025 PatSnap. All rights reserved.Legal|Privacy policy|Modern Slavery Act Transparency Statement|Sitemap|About US| Contact US: help@patsnap.com