Advanced treatment method and processing system for wastepaper pulping and papermaking waste water
A technology for pulping, papermaking and wastewater, applied in the field of circular economy and water treatment, can solve the problems of high treatment cost, easy blockage of membrane holes, and high membrane treatment cost, and achieves the effects of stable operation, convenient operation and high degree of modernization
- Summary
- Abstract
- Description
- Claims
- Application Information
AI Technical Summary
Problems solved by technology
Method used
Image
Examples
Embodiment 1
[0036] This embodiment provides an advanced treatment system for waste paper pulping and papermaking wastewater, which is used to treat waste paper pulping and papermaking wastewater treated with activated sludge method, such as figure 1 As shown, the system specifically includes:
[0037] Pre-coagulation tank, coagulation reaction tank, coagulation sedimentation tank, advanced oxidation treatment device, ozone catalytic oxidation device and biofilm contact oxidation device; the pre-coagulation tank, coagulation reaction tank, coagulation sedimentation tank, advanced The oxidation treatment device, the ozone catalytic oxidation device and the biofilm contact oxidation device are connected in sequence to form a wastewater treatment that can combine four treatment methods including coagulation sedimentation treatment, advanced oxidation treatment, ozone catalytic oxidation and biofilm contact oxidation treatment in stages system.
[0038] Wherein, the pre-coagulation tank is pr...
Embodiment 2
[0048] This embodiment provides a method for advanced treatment of waste paper pulping and papermaking wastewater. The treatment system as described in Embodiment 1 can be used to treat the reclaimed water after the waste paper pulping and papermaking wastewater has been treated by the activated sludge method. Such as figure 2 As shown, the method specifically includes the following steps:
[0049] Coagulation and sedimentation treatment: Pre-coagulation treatment is carried out on waste paper pulping and papermaking wastewater, and coagulation agents are dry-dosed into the pre-coagulation treatment wastewater. The coagulation agents are slaked lime and sodium hydroxide powder, and the mass ratio is It is 4:1 or 3:1 (actually, quicklime and caustic soda can also be used as coagulants, and the dry method is used when adding, and the mass ratio of quicklime and caustic soda can also be 4:1 or 3:1). The dosage is 0.8-1.0g / L, and the mixing time of hydraulic agitation is 5-7 min...
Embodiment 3
[0078] In this embodiment, the treatment system described in Embodiment 1 is used, combined with the treatment method described in Embodiment 2, to carry out a specific treatment process on the biochemically treated effluent discharged from a waste paper pulping and paper mill, and to make a contribution to the present invention. To further illustrate, the effluent from the biochemical reaction tank of the waste paper pulping and paper mill enters the pre-coagulation part of the coagulation and sedimentation treatment through a first-stage lift, and the mass ratio of slaked lime and sodium hydroxide is added through a dry powder doser. Powder, the dosage of dry powder is 1.0g / L, in order to achieve the purpose of destabilizing and adjusting the pH value of the solution. After stirring, the solution directly enters the coagulation reaction tank for coagulation and sedimentation treatment, and polyacrylamide is added to the coagulation reaction tank, and stirred by the impeller i...
PUM
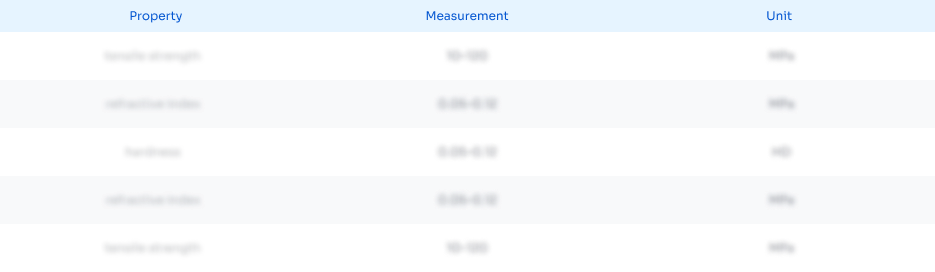
Abstract
Description
Claims
Application Information

- R&D
- Intellectual Property
- Life Sciences
- Materials
- Tech Scout
- Unparalleled Data Quality
- Higher Quality Content
- 60% Fewer Hallucinations
Browse by: Latest US Patents, China's latest patents, Technical Efficacy Thesaurus, Application Domain, Technology Topic, Popular Technical Reports.
© 2025 PatSnap. All rights reserved.Legal|Privacy policy|Modern Slavery Act Transparency Statement|Sitemap|About US| Contact US: help@patsnap.com