Machine halt energy conservation implementing method in no-load running period of adjacent process steps of numerical control machine
A technology of no-load operation and CNC machine tools, which is applied in the direction of digital control, metal processing, electrical program control, etc., can solve the problems of machine tool energy loss, low energy utilization rate of machine tools, low average energy utilization rate of machine tools, etc., and achieve energy saving of machine tools Effect
- Summary
- Abstract
- Description
- Claims
- Application Information
AI Technical Summary
Problems solved by technology
Method used
Image
Examples
Embodiment Construction
[0049] The present invention will be further described below in conjunction with a specific embodiment.
[0050] The present invention is tried out on a numerically controlled lathe that is the CK6136 that Nanjing No. 2 Machine Tool Works produces, and the trial process is as follows:
[0051] 1. Preparation of calculation formula
[0052] ① Establishment of test data table
[0053] The speed range of the lathe is 0 rpm-1500 rpm, which is divided into 10 gears, and the test collection is carried out according to the requirements of Table 1 and Table 2 respectively, and Table 3 and Table 4 are obtained.
[0054] Table 3 No-load power table of the main drive system at various spindle speeds of CNC lathes
[0055] Spindle speed (rev / min) 150 300 450 600 750 900 1050 1200 1350 1500 Machine tool main drive system
No-load power (watts)
80
120
150
173
210
230
275
300
345
365
[...
PUM
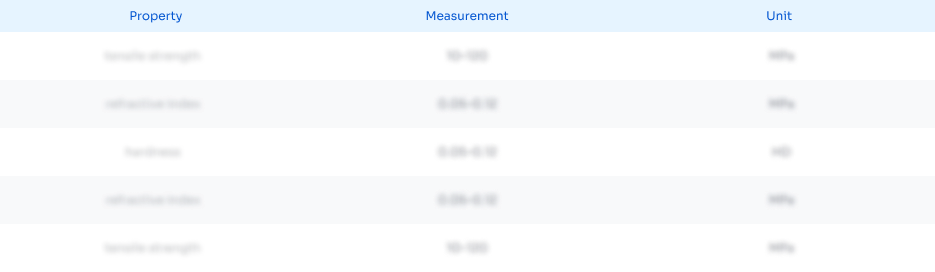
Abstract
Description
Claims
Application Information

- Generate Ideas
- Intellectual Property
- Life Sciences
- Materials
- Tech Scout
- Unparalleled Data Quality
- Higher Quality Content
- 60% Fewer Hallucinations
Browse by: Latest US Patents, China's latest patents, Technical Efficacy Thesaurus, Application Domain, Technology Topic, Popular Technical Reports.
© 2025 PatSnap. All rights reserved.Legal|Privacy policy|Modern Slavery Act Transparency Statement|Sitemap|About US| Contact US: help@patsnap.com