Ore dressing technique of microcrystal and cryptocrystal low grade collophanite ore
A cryptocrystalline, low-grade technology, applied in flotation, solid separation, etc., can solve the problems of difficult and effective utilization of middling mines, high energy consumption, and low recovery rate of phosphorous concentrate
- Summary
- Abstract
- Description
- Claims
- Application Information
AI Technical Summary
Problems solved by technology
Method used
Examples
Embodiment 1
[0015] (1) The ore mined from a certain mining area of Shimen Phosphate Mine has a grade of P 2 o 5 15.47%, harmful impurity MgO content is 9.63%, after crushing-grinding, the ore is wet-ground to -200 mesh with a fineness of 92%; It is carried out in the center, using one desliming flotation, one reverse flotation and separation operation combined with carbonate reverse flotation foam products, discharging fine mud and carbonate tailings, and the dosage of desliming flotation agent water glass is 6.5Kg / t Raw ore; the dosage of WA-3 is 0.75Kg / t raw ore; flotation time is 4 minutes; the dosage of reverse flotation beneficiation mixed acid is 1Kg / t raw ore, and the flotation time is 8 minutes; (3) Phosphate positive flotation, desliming by flotation method The product in the final tank is subjected to phosphate positive flotation. The phosphate positive flotation is carried out in an alkali-free flotation medium at 25°C. The dosage of water glass is 1Kg / t raw ore, the dosage...
Embodiment 2
[0017] (1) The ore mined from a certain mining area of Shimen Phosphate Mine has a grade of P 2 o 5 It is 15.47%, and the harmful impurity MgO content is 9.63%. After crushing-grinding, the ore is wet-ground to -200 mesh with a fineness of 92%; (2) Desliming by flotation, desliming by flotation at room temperature It is carried out in an alkali-free flotation medium, using a desliming flotation, and a reverse flotation selection operation combined with a carbonate reverse flotation foam product to discharge fine mud and carbonate tailings, and the dosage of desliming flotation agents The time and time are: the dosage of water glass is 6.5Kg / t raw ore; the dosage of WA-3 is 0.75Kg / t raw ore; the flotation time is 4 minutes; Phosphate positive flotation, the product in the tank after desliming by the flotation method is subjected to phosphate positive flotation, and the phosphate positive flotation is carried out in an alkali-free flotation medium at room temperature, and the...
Embodiment 3
[0019] (1) The ore mined from a certain mining area of Shimen Phosphate Mine has a grade of P 2 o 519.02%, the content of harmful impurity MgO is 6.92%, after crushing-grinding, the ore is wet-ground to -200 mesh with a fineness of 90%; (2) Desliming by flotation, in the process of ore grinding This part of the fine mud is preferably floated out by flotation. The desliming of the flotation method is carried out in an alkali-free flotation medium at room temperature. Flotation and concentration operation, discharging fine mud and carbonate tailings, desliming flotation water glass dosage 8.0Kg / t raw ore, WA-3 dosage 1.0Kg / t raw ore; flotation time 4 minutes; reverse flotation concentration agent mixed acid The dosage is 0.5Kg / t raw ore, and the flotation time is 10 minutes. (3) Phosphate positive flotation, the product in the tank after desliming by flotation method is subjected to phosphate positive flotation, and phosphate positive flotation is flotation without alkali at ...
PUM
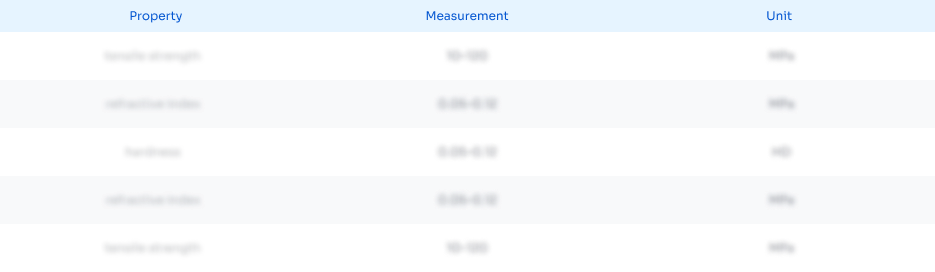
Abstract
Description
Claims
Application Information

- R&D Engineer
- R&D Manager
- IP Professional
- Industry Leading Data Capabilities
- Powerful AI technology
- Patent DNA Extraction
Browse by: Latest US Patents, China's latest patents, Technical Efficacy Thesaurus, Application Domain, Technology Topic, Popular Technical Reports.
© 2024 PatSnap. All rights reserved.Legal|Privacy policy|Modern Slavery Act Transparency Statement|Sitemap|About US| Contact US: help@patsnap.com