Radiating structure of LED
A technology of light-emitting diodes and heat-dissipating structures, which is applied to semiconductor devices of light-emitting elements, light sources, point light sources, etc., can solve the problems of low luminous efficiency, large power consumption, poor heat dissipation, etc. The effect of prolonging life
- Summary
- Abstract
- Description
- Claims
- Application Information
AI Technical Summary
Problems solved by technology
Method used
Image
Examples
Embodiment Construction
[0013] Fig. 1 is an overall assembly diagram of the heat dissipation structure of the light emitting diode of the present invention.
[0014] In the figure, the light-emitting diode heat dissipation structure includes a metal casing 1, a packaging cover 2, a light-emitting diode 3, a mirror reflector 4, an anti-leakage silicone rubber 5, a mirror reflective solid crystal heat conduction bracket 6, and a heat dissipation coolant 7. The metal casing 1 is the casing of the light-emitting diode, which is used to dissipate the heat emitted by the light-emitting diode when it is working. The packaging cover 2 is on the top of the metal shell 1 for packaging the light emitting diode 3. The light emitting diode 3 is located in the center of the mirror reflector 4. The mirror surface reflector 4 is on the upper part of the metal shell 1, and the reflection angle of the mirror surface reflector 4 is 130o-160o . The anti-leakage silicone rubber 5 is attached to the lower end of the mirror r...
PUM
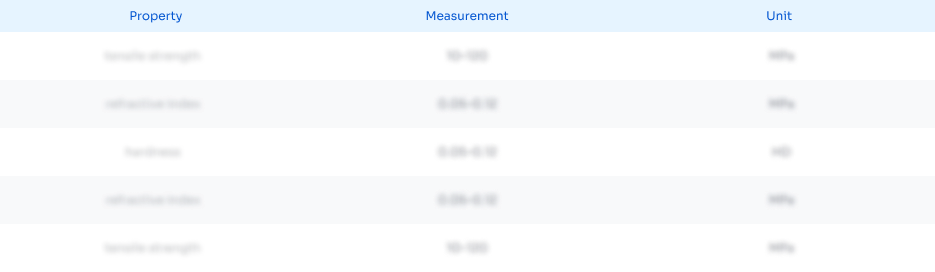
Abstract
Description
Claims
Application Information

- Generate Ideas
- Intellectual Property
- Life Sciences
- Materials
- Tech Scout
- Unparalleled Data Quality
- Higher Quality Content
- 60% Fewer Hallucinations
Browse by: Latest US Patents, China's latest patents, Technical Efficacy Thesaurus, Application Domain, Technology Topic, Popular Technical Reports.
© 2025 PatSnap. All rights reserved.Legal|Privacy policy|Modern Slavery Act Transparency Statement|Sitemap|About US| Contact US: help@patsnap.com