Mix mine groove discharge gate control apparatus, system and mix mine groove
A technology of control device and discharge door, applied in the direction of electrical program control, use feedback control, program control in sequence/logic controller, etc., can solve problems such as dust adhesion, impossibility of implementation, and influence on measurement accuracy, and achieve The effect of extending the service life, automatic and precise control, and maintaining control accuracy
- Summary
- Abstract
- Description
- Claims
- Application Information
AI Technical Summary
Problems solved by technology
Method used
Image
Examples
Embodiment Construction
[0027] The invention relates to the positioning detection and control technology of the discharge door of the mixing ore tank in the sintering process. Through the positioning detection of the discharge door of the mixing ore tank, the obtained position information and temperature information of the sinter burn-through point are used to control the mixing ore tank The opening position and degree of the discharge door make the thickness and uniformity of the mixed material arranged on the conveyor belt of the sintering machine reach ideal values, which can well balance the sintering efficiency and quality of the mixed material. In order to solve the problem of harsh on-site environment, the invention seals and integrates the detection element into the dustproof box, and is equipped with air purge and air cooling, which can effectively prevent the influence of on-site dust, high temperature and high humidity on the detection device. In the embodiment of the present invention, the...
PUM
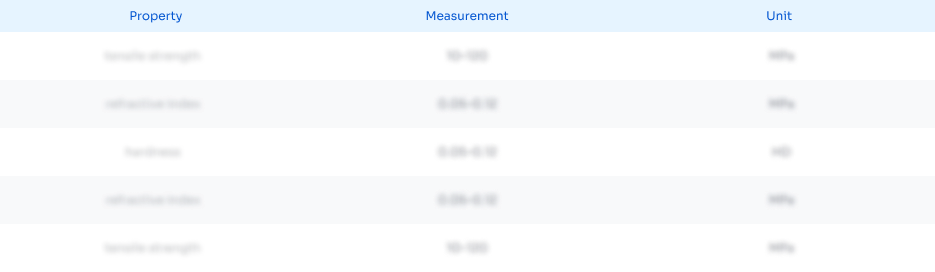
Abstract
Description
Claims
Application Information

- R&D Engineer
- R&D Manager
- IP Professional
- Industry Leading Data Capabilities
- Powerful AI technology
- Patent DNA Extraction
Browse by: Latest US Patents, China's latest patents, Technical Efficacy Thesaurus, Application Domain, Technology Topic, Popular Technical Reports.
© 2024 PatSnap. All rights reserved.Legal|Privacy policy|Modern Slavery Act Transparency Statement|Sitemap|About US| Contact US: help@patsnap.com