Process for synthesizing acrylic ester copolymer of ultra-high molecular mass
An ultra-high molecular weight, acrylate technology, applied in the field of synthesis of ultra-high molecular weight acrylate copolymers, can solve the problems of bursting kettle gel, reducing production efficiency, uncontrollable reaction temperature, etc., to improve molecular weight, reduce production efficiency, The effect of reducing labor efficiency
- Summary
- Abstract
- Description
- Claims
- Application Information
AI Technical Summary
Problems solved by technology
Method used
Examples
example 1
[0024] 1) Preparation of seed emulsion: the reaction is carried out in a cubic reactor, and 200 kg of deionized water (500 kg in total) is added to the reactor, and 150 kg of ethylenically unsaturated monomer—methyl methacrylate (500 kg in total) is added into the reactor. ), all butyl acrylate 30kg and all ethyl acrylate 20kg, add emulsifier sodium cetyl benzene sulfonate 6kg, oxidant potassium persulfate 0.144kg (total amount 0.16kg), all reducing agent sodium sulfite 0.10kg, 0.03kg of pH buffering agent sodium hydroxide, 0.000002kg of metal ion complexing agent copper sulfate and 0.000004kg of ferrous sulfate, stirring and heating up to 25°C under nitrogen protection;
[0025] 2) Segmented polymerization reaction: observe the heat released by the reaction, and when the temperature rises to 50°C, put the remaining 350kg of methyl methacrylate into 10 segments (the interval between each segment is 10 minutes, and the feeding amount of each segment is equal) into the reactor A...
example 2
[0027] 1) Preparation of seed emulsion: the reaction is carried out in a cubic reactor, and 200 kg of deionized water (500 kg in total) is added to the reactor, and 150 kg of methyl methacrylate, an ethylenically unsaturated monomer (500 kg in total), is added , all butyl acrylate 30kg and all ethyl acrylate 20kg, add emulsifier sodium lauryl sulfate 6kg, oxidant ammonium persulfate 0.144kg (total amount 0.16kg), all reducing agent sodium dithionite 0.10kg, all pH buffer Sodium hydroxide 0.03kg, add metal ion complexing agent copper sulfate 0.000002kg (all) and ferrous sulfate 0.000004kg (all), stir and heat up to 25 ℃ under nitrogen protection;
[0028] 2) Segmented polymerization reaction: observe the heat released by the reaction, and when the temperature rises to 50°C, put the remaining monomer 350kg into the reaction kettle in 5 to 30 segments (each segment is 10 minutes apart, and the feeding amount of each segment is equal) At this moment, observe that the reaction syst...
example 3
[0030] 1) Preparation of seed emulsion: the reaction is carried out in a cubic reactor, and 200 kg of deionized water (500 kg in total) is added to the reactor, and 150 kg of methyl methacrylate, an ethylenically unsaturated monomer (500 kg in total), is added , all butyl acrylate 15kg and all ethyl acrylate 20kg, all styrene 10KG, acrylic acid 5KG, add emulsifier sodium lauryl sulfate 6kg, oxidant ammonium persulfate 0.144kg (total amount 0.16kg), all reducing agent Sodium sulfite 0.10kg, all pH value buffer agent sodium hydroxide 0.03kg, add metal ion complexing agent copper sulfate 0.000002kg (all) and ferrous sulfate 0.000004kg (all), stir and heat up to 25 ℃ under nitrogen protection;
[0031] 2) Segmented polymerization reaction: observe the heat released by the reaction, and when the temperature rises to 50°C, put the remaining monomer 350kg into the reaction kettle in 5 to 30 segments (each segment is 10 minutes apart, and the feeding amount of each segment is equal) A...
PUM
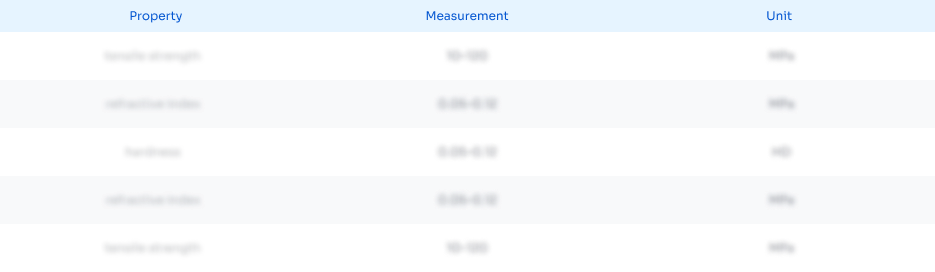
Abstract
Description
Claims
Application Information

- Generate Ideas
- Intellectual Property
- Life Sciences
- Materials
- Tech Scout
- Unparalleled Data Quality
- Higher Quality Content
- 60% Fewer Hallucinations
Browse by: Latest US Patents, China's latest patents, Technical Efficacy Thesaurus, Application Domain, Technology Topic, Popular Technical Reports.
© 2025 PatSnap. All rights reserved.Legal|Privacy policy|Modern Slavery Act Transparency Statement|Sitemap|About US| Contact US: help@patsnap.com