Rotary-screen flicker printing method on pure wax printing cloth
A rotary screen printing and printing technology, which is applied to screen printing machines, printing machines, printing machines, etc., can solve the problems of low production efficiency, high production costs, difficulty in mass production, and widespread popularization, and achieve improved printing effects, The effect of increasing the added value and improving the gear
- Summary
- Abstract
- Description
- Claims
- Application Information
AI Technical Summary
Problems solved by technology
Method used
Examples
Embodiment Construction
[0023] The following describes the specific implementation of the present invention using a rotary screen printing machine to apply the flickering printing technology to the true batik printing technology.
[0024] True batik printing is fundamentally different from other printings. True batik printing is printed on both sides of the cloth, that is, the color of the front and back is the same after printing, so it is also called through printing. In order to organically combine the true batik printing technology and the flickering printing technology, the cylinder type rotary screen printing method is selected in the present invention, thereby being different from common rotary screen printing machines. The characteristic of the cylinder type rotary screen printing machine is that it can produce double-sided printing effect (through printing effect), while the general rotary screen printing machine can only produce single-sided printing effect.
[0025] As mentioned above, th...
PUM
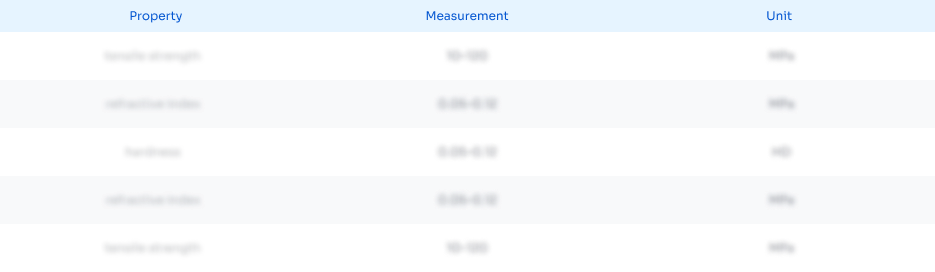
Abstract
Description
Claims
Application Information

- R&D Engineer
- R&D Manager
- IP Professional
- Industry Leading Data Capabilities
- Powerful AI technology
- Patent DNA Extraction
Browse by: Latest US Patents, China's latest patents, Technical Efficacy Thesaurus, Application Domain, Technology Topic, Popular Technical Reports.
© 2024 PatSnap. All rights reserved.Legal|Privacy policy|Modern Slavery Act Transparency Statement|Sitemap|About US| Contact US: help@patsnap.com