Preparing process of sclareol
A technology for sclareol and a preparation process is applied in the field of preparation of sclareol, can solve the problems of low product yield, long required time, influence on economic benefits and the like, and achieves high product yield, short operation time, simple craftsmanship
- Summary
- Abstract
- Description
- Claims
- Application Information
AI Technical Summary
Problems solved by technology
Method used
Image
Examples
Embodiment 1
[0022] The first step: put 200 kilograms of Sclareus extract containing 50% of sclareol into the chemical material kettle 1 with a volume of 500 liters after chopping, and then turn on the heater-7 to make the chemical material kettle 1 temperature Gradually raise the temperature to 110°C, and at the same time turn on the water ring vacuum pump SH to make the pressure of the material tank 1 reach 0.08Mpa, and extract the remaining organic solvent and volatile gas in the extract of Clary Perilla, and wait until the extract of Clary Perilla is completely melted into a liquid Phase, keep the heater a 7 constant temperature.
[0023] The second step: import the liquefied Clarisula extract into the preheated storage tank P1 with a volume of 300 liters, turn on the heater 17, and raise the temperature of the storage tank P1 to 140°C; turn on the first level Molecular distiller 3 (its evaporating surface area is 0.8 square meters, and the condensation surface area is 1.2 square meter...
Embodiment 2
[0026]In order to reach the sclareol product with an alcohol content of more than 95%, it is 90% sclareol with the alcohol content obtained by the acetone solvent and embodiment 1 in the present invention, and the sclareol with weight percentage: acetone solvent =1: 3 ratio, successively load into volume and be the airtight crystallization kettle-17 of 500 liters recrystallization. Turn on the heater two 23, under the condition of temperature 40°C-45°C, completely dissolve the sclareol in the crystallization kettle one 17, then import the completely dissolved sclareol into the crystallization kettle two 21 and let it stand still, cool down naturally After 4 hours, turn on the cooler 24 and gradually lower the temperature to -15°C; start the agitator 18 at the same time, the stirring rate is 40rpm, and it takes about 10-12 hours. Cloth filtration, the sclareol after filtering is placed in the static drying of vacuum drying cabinet 14, during drying, the pressure of vacuum dryin...
PUM
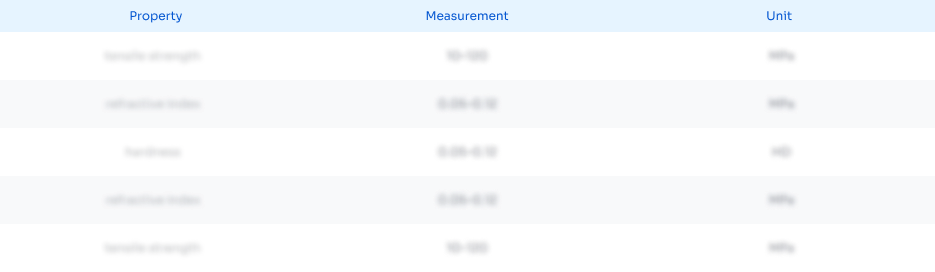
Abstract
Description
Claims
Application Information

- Generate Ideas
- Intellectual Property
- Life Sciences
- Materials
- Tech Scout
- Unparalleled Data Quality
- Higher Quality Content
- 60% Fewer Hallucinations
Browse by: Latest US Patents, China's latest patents, Technical Efficacy Thesaurus, Application Domain, Technology Topic, Popular Technical Reports.
© 2025 PatSnap. All rights reserved.Legal|Privacy policy|Modern Slavery Act Transparency Statement|Sitemap|About US| Contact US: help@patsnap.com