Diffuse multilayer optical assembly
A technology of optical components and light diffusion layers, applied in the fields of optical films and optical displays, can solve the problems of reduced revenue, reduced total output, and increased system cost
- Summary
- Abstract
- Description
- Claims
- Application Information
AI Technical Summary
Problems solved by technology
Method used
Image
Examples
example 1
[0077] The reflective polarizer used is 1 / 2 - D400, the reflective polarizing layer is 3M laminated to a sheet of approximately 130 μm thick polycarbonate (60% haze) using a radiation-curable adhesive TM Vikuiti TM Reflective Polarized Brightness Enhancement Film (DBEF-Q). Polycarbonate has a matte surface. The light-diffusing layer was a 2.0 mm light-diffusing plate with a non-uniform surface, model RM802, available from Sumitomo Chemical Company, Tokyo, Japan. The light diffusion layer includes a copolymer of methyl methacrylate and styrene (hereinafter referred to as MS). The surface properties of Surface 1 and Surface 2 of the RM802 light-diffusing layer measured using a stylus profiler are shown in Table 1 below. The reflective polarizing layer was attached to Surface 1 of the light diffusing layer using an approximately 15 μm thick layer of pressure sensitive adhesive (Adhesive A) manufactured by 3M Corporation, Saint Paul, Minnesota. Adhesive A is composed of 9...
example 2
[0081] Example 2 was prepared as described in Example 1, except that the reflective polarizing layer included approximately 250 μm thick polycarbonate layers laminated to both sides of the DBEF-Q film, and BEFIII 90 / 50 overlying one polycarbonate layer , 7R (that is, the radius of curvature is 7 μm) prism (the reflective polarizing layer is DBEF-DTV).
example 3
[0083] Example 3 was prepared as described in Example 1 except that the reflective polarizing layer used was a DBEF-Q film without the approximately 130 μm thick polycarbonate sheet laminated thereon.
PUM
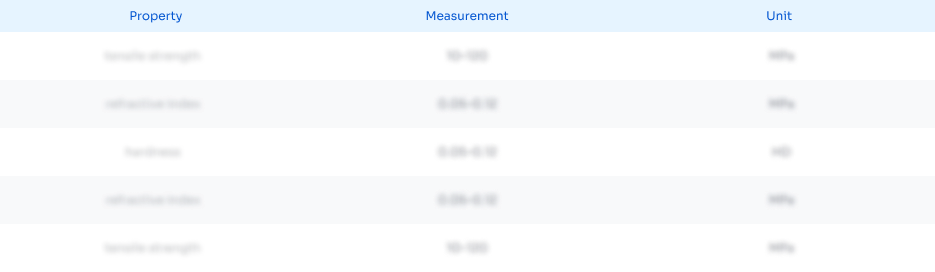
Abstract
Description
Claims
Application Information

- R&D
- Intellectual Property
- Life Sciences
- Materials
- Tech Scout
- Unparalleled Data Quality
- Higher Quality Content
- 60% Fewer Hallucinations
Browse by: Latest US Patents, China's latest patents, Technical Efficacy Thesaurus, Application Domain, Technology Topic, Popular Technical Reports.
© 2025 PatSnap. All rights reserved.Legal|Privacy policy|Modern Slavery Act Transparency Statement|Sitemap|About US| Contact US: help@patsnap.com