Process for synthesizing methyl tin chloride
A technology of monomethyltin tin trichloride and synthesis method, applied in directions such as tin organic compounds, can solve problems such as expensive catalyst price, and achieve the effects of low price, high purity, and shortening the process of synthesis
- Summary
- Abstract
- Description
- Claims
- Application Information
AI Technical Summary
Problems solved by technology
Method used
Image
Examples
Embodiment 1
[0019] Example 1: Add 119g of metal tin powder and 3g of dimethyl sulfide into a stainless steel autoclave with stirring, pass through 10g of methyl chloride and raise the temperature to 180-230°C for reaction. After the consumption of methyl chloride is complete, add 35g of tin tetrachloride, continue to add 100g of methyl chloride and react at 180-230°C for 3-6 hours, then distill under reduced pressure to obtain 262.2g of methyl tin chloride, and the reaction yield is 99.32%.
Embodiment 2
[0020] Example 2: Add 131g of metal tin powder and 3.3g of dimethyl sulfide into a stainless steel autoclave with stirring, feed 11g of methyl chloride and raise the temperature to 180-230°C for reaction. After the methyl chloride is consumed, add 38.5g of tin tetrachloride, continue to add 110g of methyl chloride, react at 180-230°C for 3-6 hours, then distill under reduced pressure to obtain 288.1g of methyl tin chloride, the reaction yield is 99.22%.
Embodiment 3
[0021] Embodiment 3: Add 154.7g of metal tin powder and 3.9g of dimethyl sulfide in a stainless steel autoclave with stirring, feed 13g of methyl chloride and heat up to 180-230°C for reaction, after the consumption of methyl chloride is completed, then Add 45.5g of tin tetrachloride, continue to add 130g of methyl chloride and react at 180-230°C for 3-6 hours, then distill under reduced pressure to obtain 340.5g of methyl tin chloride, the reaction yield is 99.18%.
[0022] In the above-mentioned embodiment:
[0023] The tin powder is in the range of 10-50 meshes, and can be firstly mixed with the solvent methyl tin chloride at a temperature of 180-200°C.
[0024] The solvent methyl tin chloride can be composed of monomethyl tin trichloride and dimethyl tin dichloride, the weight ratio of the two is 15-25: 75-85, and generally 20: 80 is used for comparison it is good.
[0025] When the present invention is reacted in a stainless steel high-pressure reactor with stirring, th...
PUM
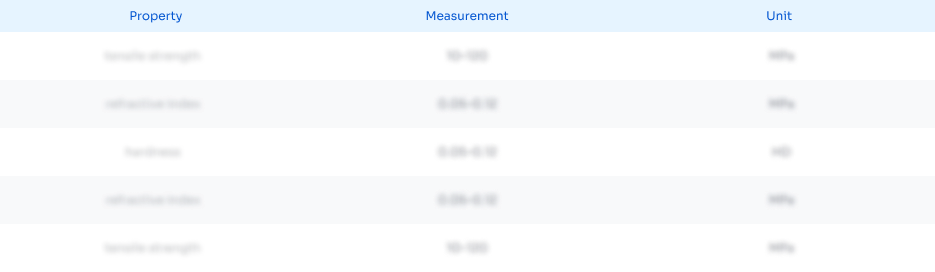
Abstract
Description
Claims
Application Information

- Generate Ideas
- Intellectual Property
- Life Sciences
- Materials
- Tech Scout
- Unparalleled Data Quality
- Higher Quality Content
- 60% Fewer Hallucinations
Browse by: Latest US Patents, China's latest patents, Technical Efficacy Thesaurus, Application Domain, Technology Topic, Popular Technical Reports.
© 2025 PatSnap. All rights reserved.Legal|Privacy policy|Modern Slavery Act Transparency Statement|Sitemap|About US| Contact US: help@patsnap.com