Repositioning connection device of positioning for flexibility and fastening for rigidity
A technology of repeated positioning and flexible connection, used in positioning devices, clamping, supporting and other directions, can solve the problems of uneven wear of the center pin and the side of the groove, out of control of the machining accuracy of the workpiece, and high requirements for the installation of the combined device, and achieve the positioning accuracy. The effect of good retention, large horizontal torque and high positioning accuracy
- Summary
- Abstract
- Description
- Claims
- Application Information
AI Technical Summary
Problems solved by technology
Method used
Image
Examples
Embodiment 1
[0053] An elastic deformation rigid clamping and repeated positioning flexible connection device is composed of a chuck, a workpiece support plate and a pull nail. The chuck includes a chuck base 1, four positioning teeth 6, 7, 8, 9, and four Z-direction stops There are 2, 3, 4, 5 and three to eight bolt holes on the moving plane, and the chuck base 1 includes a rivet hole, the chuck base 1 is cylindrical, the rivet hole is a round hole, and the rivet hole is located In the central part of the top surface, the central axis of the nail hole coincides with the central axis of the chuck base 1, and the four positioning teeth 6, 7, 8, and 9 are the first positioning tooth 6, the second positioning tooth 7, and the third positioning tooth 8 and the fourth positioning tooth 9, the four positioning teeth 6, 7, 8, 9 are arranged radially on the circumference of the top surface of the chuck base 1, and there are radial gaps between adjacent positioning teeth. There are four Z-direction...
Embodiment 2
[0055] Except following difference, all the other parts are identical with embodiment 1, and it is characterized in that, have escape groove 19 ', 20 ', 21 ', 22 ' on the bottom surface of four through grooves 23,24,25,26.
Embodiment 3
[0057] Except for the following differences, the remaining parts are exactly the same as in Embodiment 1. It is characterized in that the inclined surfaces on both sides of the four positioning teeth 6, 7, 8, 9 of the chuck and the four Z-direction stop surfaces 2, 3, 4, 5 has cleaning air holes 31a, 31b, 31c, 31d.
PUM
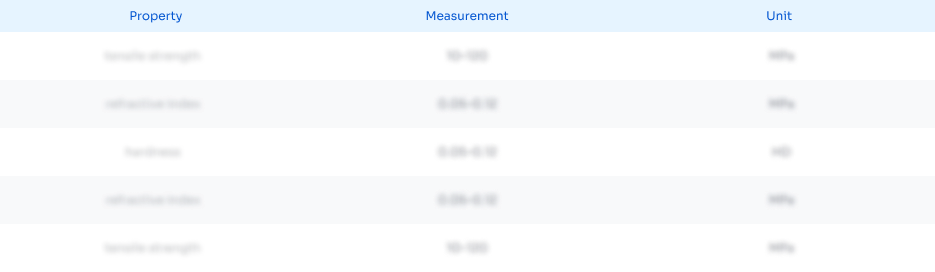
Abstract
Description
Claims
Application Information

- R&D
- Intellectual Property
- Life Sciences
- Materials
- Tech Scout
- Unparalleled Data Quality
- Higher Quality Content
- 60% Fewer Hallucinations
Browse by: Latest US Patents, China's latest patents, Technical Efficacy Thesaurus, Application Domain, Technology Topic, Popular Technical Reports.
© 2025 PatSnap. All rights reserved.Legal|Privacy policy|Modern Slavery Act Transparency Statement|Sitemap|About US| Contact US: help@patsnap.com