Automatic thickness control system for roller mill
A technology of automatic thickness control and rolling mill, applied in rolling mill control device, metal rolling, metal rolling, etc., can solve the problems of low quality and difficult to guarantee strip quality.
- Summary
- Abstract
- Description
- Claims
- Application Information
AI Technical Summary
Problems solved by technology
Method used
Image
Examples
Embodiment Construction
[0010] As shown in the drawings, the thickness automatic control system of the present invention includes a rolling mill, a computer 7, a servo mechanism 6 and a pressing cylinder 9. Servo mechanism 6 wherein is a servo valve. The rolling mill is provided with an upper work roll 10 and a lower work roll 3 . Depressing oil cylinder 9 is above rolling mill, and its piston rod is down and links to each other with the chocks at work roll 10 two ends on the rolling mill, and its oil inlet and outlet are connected with the outlet and oil inlet of servomechanism 6 by oil pipe respectively. The control end of the servomechanism 6 is connected with the computer 7 through wires. A position sensor 8 is installed on the piston rod of the depressing oil cylinder 9, and the position sensor is connected with the depressing control circuit in the computer 7 by wires. The entrance side and the exit side of the rolling mill are respectively provided with an entrance speed measuring roller 1 a...
PUM
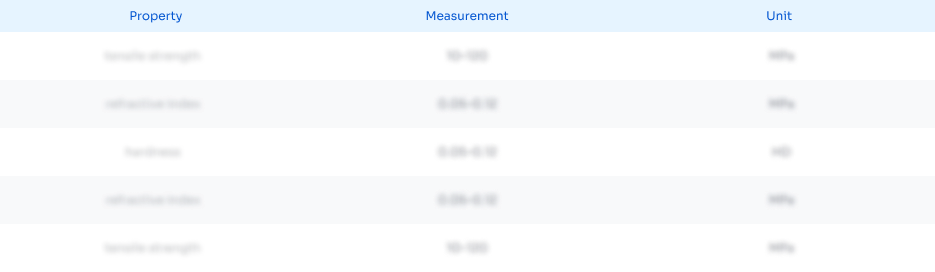
Abstract
Description
Claims
Application Information

- R&D
- Intellectual Property
- Life Sciences
- Materials
- Tech Scout
- Unparalleled Data Quality
- Higher Quality Content
- 60% Fewer Hallucinations
Browse by: Latest US Patents, China's latest patents, Technical Efficacy Thesaurus, Application Domain, Technology Topic, Popular Technical Reports.
© 2025 PatSnap. All rights reserved.Legal|Privacy policy|Modern Slavery Act Transparency Statement|Sitemap|About US| Contact US: help@patsnap.com