Optical fiber, sealing method for optical fiber end face, connection structure of optical fiber, and optical connector
An end-face sealing, optical fiber technology, applied in the direction of cladding optical fiber, optical waveguide light guide, optical waveguide coupling, etc., can solve the problems of fiber end face cracks and reduce long-term reliability.
- Summary
- Abstract
- Description
- Claims
- Application Information
AI Technical Summary
Problems solved by technology
Method used
Image
Examples
no. 1 approach
[0034]
[0035] figure 1 It is the optical fiber in 1st Embodiment of this invention, (a) is a front view, (b) is a side cross-sectional view.
[0036] This optical fiber is a holey fiber 50 composed of a solid core 11, a cladding 12 disposed around the core 11, and a plurality of holes 13 having a refractive index of approximately 1 disposed around the core 11. The holey fiber 50 It also includes a curable resin 15 filled in the cavity 13 of the optical fiber end face 14 . exist figure 1 In (a) and (b), the end face of the core 11 is provided so as to form the same plane as the end face of the holey fiber 50 .
[0037] The curable resin 15 used has a moisture permeability of 0.5 g / cm after curing 2 ·Characteristics below 24h. If the moisture permeability of curable resin 15 is greater than 0.5g / cm 2 ·24h, in an environment with high humidity, dew condensation and the like are likely to occur in the cavity 13, and the loss is likely to increase. Preferably, the moistur...
Embodiment
[0049] Next, examples of the present invention will be described. Fig. 2 is a characteristic diagram showing optical fiber connection loss characteristics in the first embodiment.
[0050] As shown in the figure, an SC (Single Coupling) type connector is attached to the end of a holey optical fiber 50 whose cavity 13 is sealed with a curable resin 15, and an optical fiber equipped with a general-purpose SC connector on a normal SMF is connected to the end of the holey optical fiber 50. Changes in the connection loss of the holey fiber 50 when the connection part is placed in a constant temperature bath and subjected to a temperature-humidity cycle test (-40 to +70° C., 93% RH).
[0051] In Figure 2, the moisture permeability of Example 1 is 0.21g / cm 2 24h, the moisture permeability of Example 2 is 0.36g / cm 2 24h, the moisture permeability of Comparative Example 1 is 0.64g / cm 2 24h.
[0052] It can be seen from FIG. 2 that the connection loss of Comparative Example 1 having...
PUM
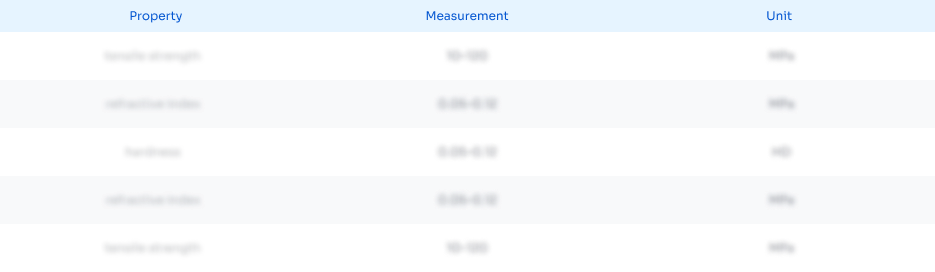
Abstract
Description
Claims
Application Information

- Generate Ideas
- Intellectual Property
- Life Sciences
- Materials
- Tech Scout
- Unparalleled Data Quality
- Higher Quality Content
- 60% Fewer Hallucinations
Browse by: Latest US Patents, China's latest patents, Technical Efficacy Thesaurus, Application Domain, Technology Topic, Popular Technical Reports.
© 2025 PatSnap. All rights reserved.Legal|Privacy policy|Modern Slavery Act Transparency Statement|Sitemap|About US| Contact US: help@patsnap.com