Machining method of shielding motor rotor
A processing method and shielded motor technology, which is applied in the manufacture of motor generators, stator/rotor bodies, electrical components, etc., can solve the problems of shielding sleeve damage, moisture ingress, etc., and achieve the effect of eliminating quality problems
Active Publication Date: 2008-11-19
HEFEI XINHU CANNED MOTOR PUMP
View PDF0 Cites 8 Cited by
- Summary
- Abstract
- Description
- Claims
- Application Information
AI Technical Summary
Problems solved by technology
This processing technology has certain defects, that is, it is easy to enter the moisture from the leak detection hole 1 during the processing, and the moisture will be stored in the rotor shielding sleeve 4 after sealing, and the moisture will be heated and expanded during actual operation after leaving the factory to shield it. Set 4 starts to rub against the shielding sleeve of the stator, causing damage to the shielding sleeve and causing certain quality problems
Method used
the structure of the environmentally friendly knitted fabric provided by the present invention; figure 2 Flow chart of the yarn wrapping machine for environmentally friendly knitted fabrics and storage devices; image 3 Is the parameter map of the yarn covering machine
View moreImage
Smart Image Click on the blue labels to locate them in the text.
Smart ImageViewing Examples
Examples
Experimental program
Comparison scheme
Effect test
Embodiment Construction
the structure of the environmentally friendly knitted fabric provided by the present invention; figure 2 Flow chart of the yarn wrapping machine for environmentally friendly knitted fabrics and storage devices; image 3 Is the parameter map of the yarn covering machine
Login to View More PUM
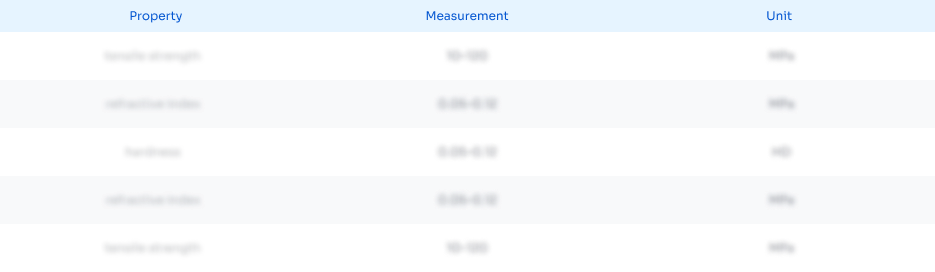
Abstract
Disclosed is a processing method for shielding a motor rotator. Two shielding plates are covered on the shaft when a rotator is processed by rough machining; then the connection part between the shaft and the shielding plate is processed by argon arc welding; then a stainless steel thread is welded by fusion welding on the base to achieve a sealing function; then the rotator is processed by finish machining and a rotator shield cover is installed; and then the rotator is put into an oven and kept at the temperature of 250 DEG C for 4-5 hours to vaporize the moisture out of the rotator inner cavity from the leakage detecting hole by high temperature; after that, the rotator is taken out and the leakage detecting hole is immediately sealed by argon arc welding; and then the rotator can be moved to following processes. Compared with prior art, firstly, the method solves the problem of leaving moisture in the rotator and effectively avoids the bulge phenomena of the rotator shield cover; secondly, the rotator is sealed after being in 250 DEG C for long time, the shield cover can shrink and closely cling to the outer diameter of the rotator iron core after cooling, making the place thereof gapless; moreover, the shield cover will not distort in the future when the pump works because the shield cover performs a certain of thermal expansion and cooling contraction at the situation above the working status.
Description
A processing method for a shielded motor rotor technical field The invention relates to the technical field of electromechanical equipment manufacturing, in particular to a processing method for a shielded motor rotor. Background technique Shielded motors are generally used to be installed on various types of HVAC pumps, but due to existing processing technology problems, the rotor shielding sleeve often expands or bulges after the motor has been used for a period of time, causing various problems. Referring to Figure 1, the rotor of the shielded motor includes a shaft 5 with an iron core 6 on the shaft, screen plates 2 and 3 at both ends of the iron core 6, and a shielding sleeve 4 on the outer side of the iron core 6. The processing method is generally two rotors The screen plates 2 and 3 are hot-installed on the shaft 5 shown in Fig. 1 in time after being heated at high temperature, and after the natural cooling, the inner diameter of the screen board shrinks to clamp ...
Claims
the structure of the environmentally friendly knitted fabric provided by the present invention; figure 2 Flow chart of the yarn wrapping machine for environmentally friendly knitted fabrics and storage devices; image 3 Is the parameter map of the yarn covering machine
Login to View More Application Information
Patent Timeline

Patent Type & Authority Applications(China)
IPC IPC(8): H02K15/02H02K15/12
Inventor 韩元平
Owner HEFEI XINHU CANNED MOTOR PUMP
Features
- R&D
- Intellectual Property
- Life Sciences
- Materials
- Tech Scout
Why Patsnap Eureka
- Unparalleled Data Quality
- Higher Quality Content
- 60% Fewer Hallucinations
Social media
Patsnap Eureka Blog
Learn More Browse by: Latest US Patents, China's latest patents, Technical Efficacy Thesaurus, Application Domain, Technology Topic, Popular Technical Reports.
© 2025 PatSnap. All rights reserved.Legal|Privacy policy|Modern Slavery Act Transparency Statement|Sitemap|About US| Contact US: help@patsnap.com