Process for preparing titanium dioxide nano-belts
A titanium dioxide, nanobelt technology, applied in the field of nanomaterials
- Summary
- Abstract
- Description
- Claims
- Application Information
AI Technical Summary
Problems solved by technology
Method used
Image
Examples
Embodiment 1
[0018] Example 1: Weigh 5.0g of butyl titanate, dissolve it in 35.5g of chloroform, then weigh 3.0g of PMMA and 1.5g of PVP and add them to the above-mentioned butyl titanate in chloroform solution, finally add 5.0g of DMF, and After magnetic stirring at room temperature for 8 hours and then standing for 4 hours, a uniform, transparent and viscous Ti(OC 4 h 9 ) 4 / (PMMA+PVP) spinning solution. The weight ratio of each component of the spinning solution is: 10% of butyl titanate, 3% of PVP, 6% of PMMA, 71% of chloroform and 10% of DMF. Add the prepared spinning solution into the liquid storage tube of the spinning device for electrospinning, the nozzle diameter is 1mm, the angle between the nozzle and the horizontal plane is adjusted to 30°, a DC voltage of 20kV is applied, the curing distance is 21cm, and the room temperature is 25°C , with a relative humidity of 55%, Ti(OC 4 h 9 ) 4 / (PMMA+PVP) composite nanobelts. The prepared Ti(OC 4 h 9 ) 4 / (PVP+PMMA) composite ...
Embodiment 2
[0019] Embodiment 2: take by weighing 7.5g titanium isopropoxide (Ti(OC 3 h 7 ) 4 ), dissolved in 32g of chloroform, then weighed 3.5g of PMMA and 2.5g of PVP and added them to the chloroform solution of titanium isopropoxide, then added 4.5g of DMF, stirred magnetically at room temperature for 10h and left it for 10h to obtain Uniform, transparent, Ti(OC) with a certain viscosity 3 h 7 ) 4 / (PMMA+PVP) spinning solution. The weight ratio of each component of the spinning solution is: titanium isopropoxide 15%, PVP 5%, PMMA 7%, chloroform 64%, DMF 9%. Add the prepared spinning solution into the liquid storage tube of the spinning device for electrospinning, the nozzle diameter is 1mm, the angle between the nozzle and the horizontal plane is adjusted to 30°, a DC voltage of 25kV is applied, the curing distance is 30cm, and the room temperature is 30°C , with a relative humidity of 65%, Ti(OC 3 h 7 ) 4 / (PMMA+PVP) composite nanobelts. The prepared Ti(OC 3 h 7 ) 4 / (P...
Embodiment 3
[0020] Embodiment 3: take by weighing 4.0g titanium tert-amyloxide (Ti(OC 5 h 11 ) 4 ), dissolved in 36.5g chloroform, then weighed 2.5g PMMA and 2.0g PVP and added to the chloroform solution of the above-mentioned titanium tert-amyloxide, then added 5.0g DMF, stirred magnetically at room temperature for 4h and left it standing for 2h, namely Uniform, transparent and viscous Ti(OC 5 h 11 ) 4 / (PMMA+PVP) spinning solution. The weight ratio of each component of the spinning solution is: titanium tert-amylate 8%, PVP 4%, PMMA 5%, chloroform 73%, DMF 10%. Add the prepared spinning solution into the liquid storage tube of the spinning device for electrospinning, the nozzle diameter is 1mm, the angle between the nozzle and the horizontal plane is adjusted to 30°, a DC voltage of 15kV is applied, the curing distance is 15cm, and the room temperature is 18°C , with a relative humidity of 45%, Ti(OC 5 h 11 ) 4 / (PMMA+PVP) composite nanobelts. The prepared Ti(OC 5 h 11 ) 4 ...
PUM
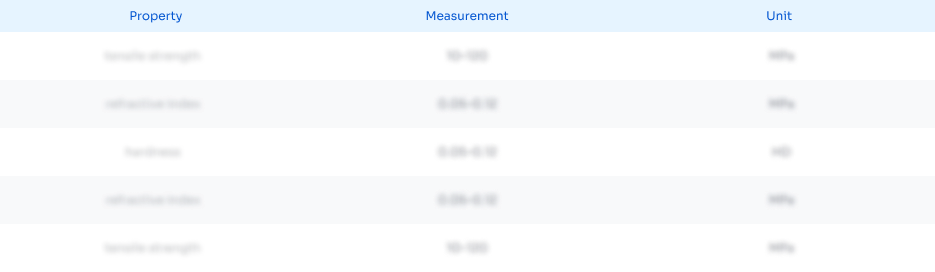
Abstract
Description
Claims
Application Information

- R&D
- Intellectual Property
- Life Sciences
- Materials
- Tech Scout
- Unparalleled Data Quality
- Higher Quality Content
- 60% Fewer Hallucinations
Browse by: Latest US Patents, China's latest patents, Technical Efficacy Thesaurus, Application Domain, Technology Topic, Popular Technical Reports.
© 2025 PatSnap. All rights reserved.Legal|Privacy policy|Modern Slavery Act Transparency Statement|Sitemap|About US| Contact US: help@patsnap.com