Method for manufacturing fixed seat with necking
A manufacturing method and technology for a fixed seat, which are applied to building structures, building components, walls, etc., can solve the problems of production or installation errors, increased material costs and production costs, detachment of universal ball joints, etc., and improve installation adaptability. , the effect of saving material costs and production costs
- Summary
- Abstract
- Description
- Claims
- Application Information
AI Technical Summary
Problems solved by technology
Method used
Image
Examples
Embodiment Construction
[0016] The present invention will be further described below in conjunction with the accompanying drawings and specific embodiments.
[0017] Such as figure 1 Shown, a kind of manufacturing method with shrinkage fixing seat, this method comprises the following steps,
[0018] A: Cut out the blanking plate from the blank;
[0019] B: Stamping and forming the blanking plate to obtain a semi-finished product of the fixing seat with a shrinkage;
[0020] C: Plasticizing the semi-finished product of the fixing seat obtained in step B.
[0021] Steps D and D are also included: heat treatment is performed after the plastic treatment in step C, and the heat treatment is solution heat treatment.
[0022] In the above steps, step B further includes the following steps,
[0023] B1: Stretch a cylinder from the blanking plate;
[0024] B2: a pit is stretched inward at the bottom of the cylinder;
[0025] B3: Make a hole in the center of the pit; the hole is punched or drilled;
[0...
PUM
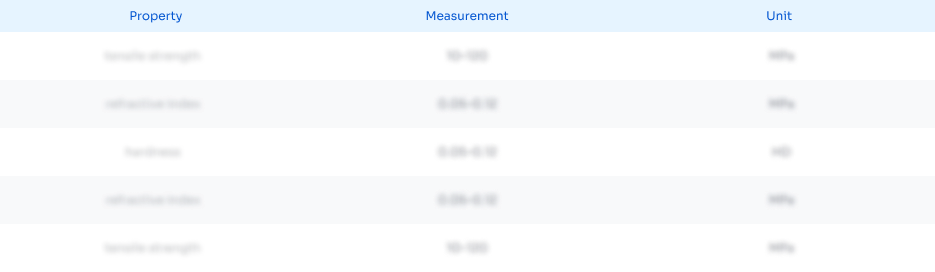
Abstract
Description
Claims
Application Information

- R&D
- Intellectual Property
- Life Sciences
- Materials
- Tech Scout
- Unparalleled Data Quality
- Higher Quality Content
- 60% Fewer Hallucinations
Browse by: Latest US Patents, China's latest patents, Technical Efficacy Thesaurus, Application Domain, Technology Topic, Popular Technical Reports.
© 2025 PatSnap. All rights reserved.Legal|Privacy policy|Modern Slavery Act Transparency Statement|Sitemap|About US| Contact US: help@patsnap.com