Method for processing collecting tube of heat exchanger
A processing method and heat exchanger technology, applied in the direction of heat exchange equipment, etc., can solve the problems of large punch press investment, complicated mold replacement, poor mold versatility, etc., achieve simple operation process, save mold costs, stamping equipment costs and operating costs Effect
- Summary
- Abstract
- Description
- Claims
- Application Information
AI Technical Summary
Problems solved by technology
Method used
Image
Examples
Embodiment Construction
[0018] The present invention will be further described below in conjunction with the accompanying drawings and specific embodiments.
[0019] Depend on figure 1 The schematic diagram of the structure of the all-aluminum brazed heat exchanger can be seen. Usually, the heat exchanger is assembled by the cover 1, the header 2, the flat tube 3, and the spacer 5. During production, one side of the header is first assembled according to the set The hole spacing and hole size of the flow tube are punched with a punching knife, and then the flat tube 3 is inserted into the punched hole of the flow tube, and sealed by brazing.
[0020] figure 2 It is a schematic diagram of the processing method of the header, as can be seen from the figure, the processing method of the header for the heat exchanger:
[0021] 1) The manifold 3 is limited between the demoulding block 8 and the lower base 9, one or more pairs of punching knives 7 are placed vertically directly above the manifold 3, and...
PUM
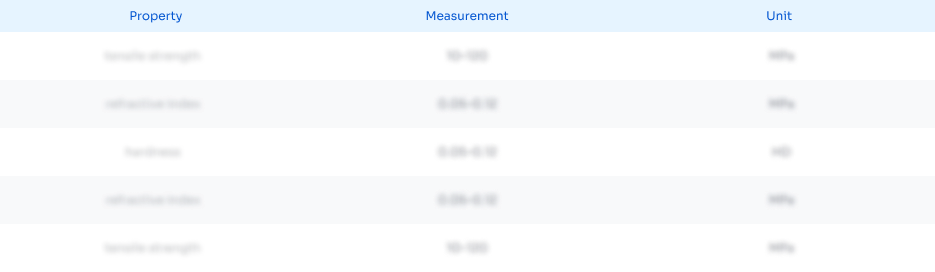
Abstract
Description
Claims
Application Information

- R&D
- Intellectual Property
- Life Sciences
- Materials
- Tech Scout
- Unparalleled Data Quality
- Higher Quality Content
- 60% Fewer Hallucinations
Browse by: Latest US Patents, China's latest patents, Technical Efficacy Thesaurus, Application Domain, Technology Topic, Popular Technical Reports.
© 2025 PatSnap. All rights reserved.Legal|Privacy policy|Modern Slavery Act Transparency Statement|Sitemap|About US| Contact US: help@patsnap.com