Steel plate cooling control analog system and method
A cooling control and simulation system technology, applied in general control systems, control/regulation systems, simulators, etc., can solve problems such as difficult to achieve general control technology engineering research, no sensors and controllers, production line debugging risks, etc. , to achieve the effect of automatic optimization setting control, saving production debugging costs, and saving online debugging time
- Summary
- Abstract
- Description
- Claims
- Application Information
AI Technical Summary
Benefits of technology
Problems solved by technology
Method used
Image
Examples
example
[0060] When the thickness of the steel plate is 25.35mm, the width is 3857mm, the length is 21559mm, the outlet temperature of the rolling mill is 793±5°C, the cooling target temperature is 530°C, the cooling rate is 20K / S, the steel type is given, the control amount and electromotive potential set by the process control device The actual flow rate fed back by the controller is as follows:
[0061] header number
[0062]After the PLC receives the set value of the process control device, press the start button, the motor refreshes the speed according to the 500ms cycle (set speed = 12mm / s), the motor drives the belt to rotate, and the steel bar mounted on the belt starts to move. When the head of the simulated steel plate moves to the first photoelectric switch position, the electric potentiometer for analog flow adjustment and electric potentiometer for analog shielding start to move, reaching the position required by the setting of flow rate and edge shielding. When...
PUM
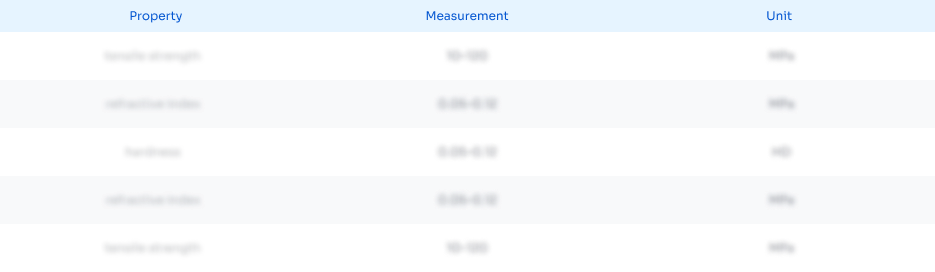
Abstract
Description
Claims
Application Information

- Generate Ideas
- Intellectual Property
- Life Sciences
- Materials
- Tech Scout
- Unparalleled Data Quality
- Higher Quality Content
- 60% Fewer Hallucinations
Browse by: Latest US Patents, China's latest patents, Technical Efficacy Thesaurus, Application Domain, Technology Topic, Popular Technical Reports.
© 2025 PatSnap. All rights reserved.Legal|Privacy policy|Modern Slavery Act Transparency Statement|Sitemap|About US| Contact US: help@patsnap.com