Laser holograph mould pressing method
A laser holography and molding technology, applied in decorative arts, printing, printing devices, etc., can solve problems such as adverse effects on product quality, inaccurate pressure changes, 08 indentation of molding materials, etc. Stable, good product quality effect
- Summary
- Abstract
- Description
- Claims
- Application Information
AI Technical Summary
Problems solved by technology
Method used
Image
Examples
Embodiment Construction
[0024] Such as image 3 As shown, the laser hologram embossing device adopted in this embodiment includes a plate roller 1, two pressing rollers (i.e. pressing roller 31 and pressing roller 32) and two back pressing rollers (i.e. back pressing roller 41 and back pressing roller 42).
[0025] refer to Figure 4 , the surface of the version roller 1 is divided into a high temperature zone 11 whose temperature reaches the molding working temperature and a low temperature zone 12 whose temperature is lower than the molding working temperature. Parallel straight lines 15 and 16; where the high temperature region 11 occupies four sevenths of the surface of the plate roller 1, and the low temperature region 12 accounts for three sevenths of the surface of the plate roller 1, that is, the central angle α1 corresponding to the high temperature region 11 is about 205.7° , the central angle α2 corresponding to the low temperature region 12 is about 154.3°.
[0026] There are two tempe...
PUM
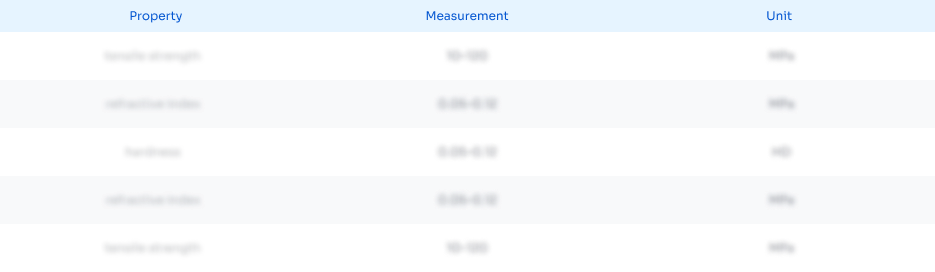
Abstract
Description
Claims
Application Information

- R&D
- Intellectual Property
- Life Sciences
- Materials
- Tech Scout
- Unparalleled Data Quality
- Higher Quality Content
- 60% Fewer Hallucinations
Browse by: Latest US Patents, China's latest patents, Technical Efficacy Thesaurus, Application Domain, Technology Topic, Popular Technical Reports.
© 2025 PatSnap. All rights reserved.Legal|Privacy policy|Modern Slavery Act Transparency Statement|Sitemap|About US| Contact US: help@patsnap.com