Tubular product internal high-pressure forming special-shaped cross section sealing method and sealing punch
A technology of internal high-pressure forming and special-shaped cross-section, which is applied in the direction of forming tools, engine seals, engine components, etc., can solve the problems of mold and pipe waste, and achieve the effects of short sealing section, energy saving, and tube blank material saving
- Summary
- Abstract
- Description
- Claims
- Application Information
AI Technical Summary
Problems solved by technology
Method used
Image
Examples
specific Embodiment approach 1
[0010] Specific embodiment 1: As shown in Fig. 1 and Fig. 2, the sealing method of high-pressure forming special-shaped cross-section in a pipe of this embodiment is realized according to the following steps: 1. Pre-deform the end cross-section of the tube blank so that the end cross-section becomes The shape is the same as or similar to the cross section of the mold cavity, then the tube blank is placed in the lower mold and the upper mold is closed; 2. The two ends of the tube blank are directly sealed with sealing punches, and liquid is filled into the tube blank; 3. The blank tube is pressurized from 0 to 400 MPa and the sealing punches at both ends of the blank tube are simultaneously pushed inward along the axial direction of the tube blank; fourth, the pressure is relieved and the sealing punch of the special-shaped section is returned to position, that is, the required workpiece is formed.
specific Embodiment approach 2
[0011] Specific implementation manner 2: As shown in Figure 1 and Figure 2, the sealing punch of this embodiment is composed of a correcting section 2, a sealing section 3, and a sealing connecting rod 4. The correcting section 2, the sealing section 3 and the sealing connecting rod 4 The front end of the correcting section 2 is fixed in order to form a whole body. The front end of the correcting section 2 is provided with a transition fillet 1. The cross-sectional area of the sealing section 3 is smaller than the cross-sectional area of the sealing connecting rod 4, and the cross-sectional area of the correcting section 2 is smaller than the cross-sectional area of the sealing connecting rod 4. The cross-sectional area gradually increases from the non-connected end to the connected end. The connecting rod 4 is connected with other driving devices, such as a plunger cylinder, etc., and the sealing load is applied by the movement of the driving device.
specific Embodiment approach 3
[0012] Specific implementation manner three: such as Figure 3~4 As shown, the cross section of the sealing punch of this embodiment is rectangular. This design is suitable for sealing when the cross section of the part to be processed is rectangular. The other composition and connection relationship are the same as in the second embodiment.
PUM
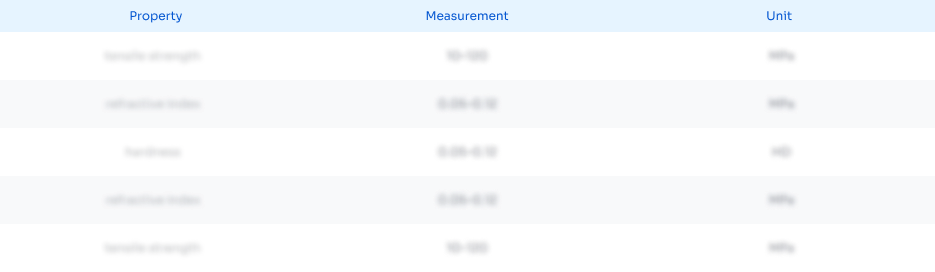
Abstract
Description
Claims
Application Information

- R&D Engineer
- R&D Manager
- IP Professional
- Industry Leading Data Capabilities
- Powerful AI technology
- Patent DNA Extraction
Browse by: Latest US Patents, China's latest patents, Technical Efficacy Thesaurus, Application Domain, Technology Topic, Popular Technical Reports.
© 2024 PatSnap. All rights reserved.Legal|Privacy policy|Modern Slavery Act Transparency Statement|Sitemap|About US| Contact US: help@patsnap.com