Backing board for laminating covered copper plate
A technology of copper clad laminate and backing plate, applied in the direction of lamination, lamination device, press, etc., can solve the problems of thinning thickness, unqualified products, etc., to reduce the thickness difference, excellent buffer, and improve the thickness qualification rate. Effect
- Summary
- Abstract
- Description
- Claims
- Application Information
AI Technical Summary
Problems solved by technology
Method used
Image
Examples
Embodiment 1
[0022] See Figure 3. During the processing of copper clad laminates, the greater the pressure on the board surface, the greater the glue flow of the bonding sheet. The size of the glue flow of the bonding sheet can be controlled by changing the pressure on each part of the board surface. , reduce the flow of glue on the edge of the board to increase the thickness of the edge of the board, reduce the thickness difference between the edge of the board and the middle of the board, and ensure the uniformity of the thickness of the entire effective area of the copper clad laminate. And changing the pressure distribution on the plate surface can be realized by changing the thickness distribution of the cushioning material. A buffer material for copper clad laminates, including a square buffer material substrate 1, the thickness of the substrate 1 linearly decreases from the middle to the periphery according to a linear function, such as decreasing according to Y=2(1-X), where Y is...
Embodiment 2
[0024] See Figure 4. During the processing of copper clad laminates, the greater the pressure on the board surface, the greater the glue flow of the bonding sheet. The size of the glue flow of the bonding sheet can be controlled by changing the pressure of each part of the board surface. , reduce the flow of glue on the edge of the board to increase the thickness of the edge of the board, reduce the thickness difference between the edge of the board and the middle of the board, and ensure the uniformity of the thickness of the entire effective area of the copper clad laminate. And changing the pressure distribution on the plate surface can be realized by changing the thickness distribution of the cushioning material. A buffer material for lamination of copper clad laminates, comprising a cuboid buffer material matrix 1, the thickness of the matrix 1 decreases stepwise from the middle to the periphery, and the decreasing range is 30% of the matrix. When every step is reduced,...
Embodiment 3
[0026] See Figure 5. During the processing of copper clad laminates, the greater the pressure on the board surface, the greater the glue flow of the bonding sheet. The size of the glue flow of the bonding sheet can be controlled by changing the pressure of each part of the board surface. , reduce the flow of glue on the edge of the board to increase the thickness of the edge of the board, reduce the thickness difference between the edge of the board and the middle of the board, and ensure the uniformity of the thickness of the entire effective area of the copper clad laminate. And changing the pressure distribution on the plate surface can be realized by changing the thickness distribution of the cushioning material. A buffer material for copper clad laminates, including a cuboid buffer material substrate 1, the thickness of the substrate 1 decreases in a non-step manner from the middle to the periphery, and the decreasing range is 50% of the substrate. The buffer material is...
PUM
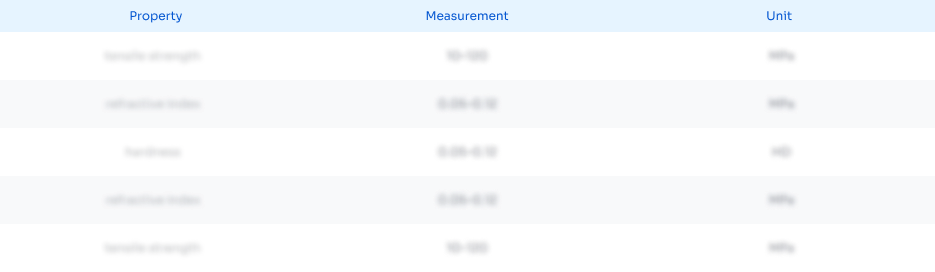
Abstract
Description
Claims
Application Information

- R&D Engineer
- R&D Manager
- IP Professional
- Industry Leading Data Capabilities
- Powerful AI technology
- Patent DNA Extraction
Browse by: Latest US Patents, China's latest patents, Technical Efficacy Thesaurus, Application Domain, Technology Topic, Popular Technical Reports.
© 2024 PatSnap. All rights reserved.Legal|Privacy policy|Modern Slavery Act Transparency Statement|Sitemap|About US| Contact US: help@patsnap.com