Preparation method of tall oil modified alkyd resin
A technology of phenolic resin and tall oil, which is applied in the field of preparation of tall oil modified phenolic resin, can solve the problem of low scorch performance, and achieve the effects of simple process, improved product performance and increased production cost
- Summary
- Abstract
- Description
- Claims
- Application Information
AI Technical Summary
Problems solved by technology
Method used
Examples
Embodiment 1
[0018] Add 90g of phenol, 6g of tert-butylphenol, and 0.4g of catalyst (oxalic acid) into a 500mL three-necked flask, raise the temperature to 50°C, stir evenly, add 55g of 37% formaldehyde dropwise under reflux, and finish adding in about 1 hour, at 102°C Reflux for 3 hours. Heating and dehydration, when the system is 110°C, it becomes transparent, continue to heat up to 130°C, stop heating, stir for 15 minutes, heat up to maintain the dehydration state, start adding 38g of rosin oil dropwise at 160°C (30g of tall oil and 8g of rosin are heated and melted in advance) , 30 minutes to add. Continue to react at 180°C for 1 hour, add N 3 P 3 (OC 6 h 4 CHO) 6 0.1 g, vacuum dehydrated for 30 minutes (vacuum degree > 0.085 MPa), stopped the reaction, poured out the material, and obtained a reddish-brown transparent flaky solid after cooling.
Embodiment 2
[0020] Add 100g of phenol, 9g of tert-butylphenol, and 0.5g of catalyst (oxalic acid) into a 1L three-necked flask, raise the temperature to 50°C, stir evenly, add 65g of 37% formaldehyde dropwise under reflux, and finish adding in 1 hour and 10 minutes, 102 °C for 3 hours at reflux. Heating and dehydration, when the system is 110°C, it becomes transparent, continue to heat up to 130°C, stop heating, stir for 15 minutes, heat up to maintain the dehydration state, start adding 50g of rosin oil dropwise at 160°C (40g of tall oil and 10g of rosin are heated and melted in advance) , 30 minutes to add. Continue to react at 180°C for 1 hour, add N 3 P 3 (OC 6 h 4 CHO) 6 0.2 g, dehydrated in vacuum for 30 minutes (vacuum degree > 0.085 MPa), stopped the reaction, poured out the material, and obtained a reddish-brown transparent flaky solid after cooling.
Embodiment 3
[0022] Add 95kg of phenol, 7.5kg of tert-butylphenol, and 0.45g of catalyst (oxalic acid) into a 200L reactor, heat up to 50°C, start stirring, add 60kg of 37% formaldehyde dropwise under reflux, and finish adding in 1 hour and 30 minutes, 102 °C for 3 hours at reflux. After the reaction is over, adjust the reflux state to the dehydration state, heat up to 130°C, stop the heat rise, stir for 15 minutes, continue to heat up to maintain the dehydration state, and start to add 44kg of rosin oil dropwise at 160°C (35kg tall oil and 9kg rosin are added dropwise in advance. In the kettle, the temperature was raised to 130-150°C), and the addition was completed in 30 minutes. Raise the temperature to 180°C and continue the reaction for 1 hour, add N 3 P 3 (OC6H4CHO) 6 0.15 g, vacuum dehydrated for 30 minutes (vacuum degree > 0.085 MPa), and discharged to obtain a reddish-brown transparent flaky solid.
PUM
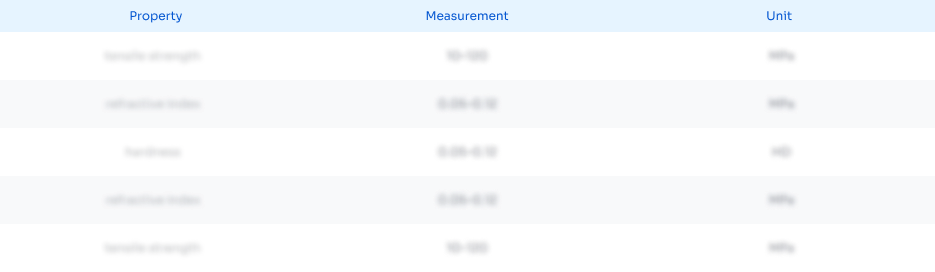
Abstract
Description
Claims
Application Information

- R&D
- Intellectual Property
- Life Sciences
- Materials
- Tech Scout
- Unparalleled Data Quality
- Higher Quality Content
- 60% Fewer Hallucinations
Browse by: Latest US Patents, China's latest patents, Technical Efficacy Thesaurus, Application Domain, Technology Topic, Popular Technical Reports.
© 2025 PatSnap. All rights reserved.Legal|Privacy policy|Modern Slavery Act Transparency Statement|Sitemap|About US| Contact US: help@patsnap.com