Radial-axial mixed magnetic bearing driven by radial quadrupole biphase alternating current
A technology of axial mixing and AC drive, which is applied in the direction of shafts and bearings, bearings, mechanical equipment, etc., can solve problems such as unspecified magnetic poles, and achieve the effects of simplifying drive control methods, reducing weight, and saving energy
- Summary
- Abstract
- Description
- Claims
- Application Information
AI Technical Summary
Problems solved by technology
Method used
Image
Examples
Embodiment Construction
[0023] The present invention first constructs a radial-axial hybrid magnetic bearing structure and magnetic circuit driven by radial four-pole two-phase AC, and constructs its mathematical model according to the equivalent magnetic circuit method. Based on this mathematical model combined with the predetermined design parameters, the structural parameters and electrical parameters of the magnetic bearing are formulated and calculated, and a magnetic bearing with excellent performance that meets the requirements of practical applications is designed according to this formula. According to the structural parameters, Maxwell 3D in the finite element analysis software ANSOFT software is used to further optimize the design of the magnetic bearing structural parameters, and verify the correctness of the structural design principles and magnetic flux distribution. Finally, according to the mathematical model and various actual parameters, the controller is designed, and the (displacem...
PUM
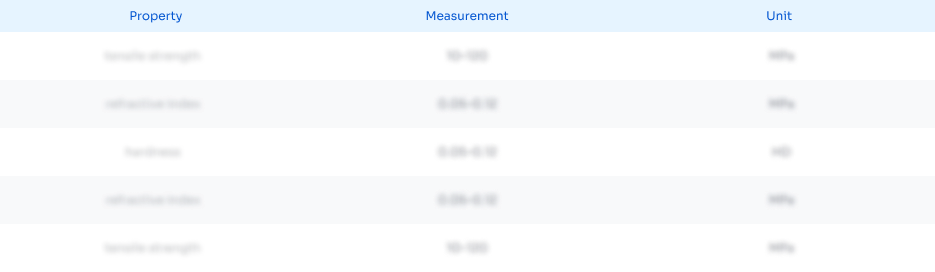
Abstract
Description
Claims
Application Information

- R&D
- Intellectual Property
- Life Sciences
- Materials
- Tech Scout
- Unparalleled Data Quality
- Higher Quality Content
- 60% Fewer Hallucinations
Browse by: Latest US Patents, China's latest patents, Technical Efficacy Thesaurus, Application Domain, Technology Topic, Popular Technical Reports.
© 2025 PatSnap. All rights reserved.Legal|Privacy policy|Modern Slavery Act Transparency Statement|Sitemap|About US| Contact US: help@patsnap.com