A PFC circuit with current sharing control module and the corresponding current sharing control method
A current control and circuit technology, which is applied in the field of two-way parallel boost PFC circuit and its current sharing control, can solve the problems of PFC circuit hardware circuit complexity, poor inductor current sharing characteristics, and inability to achieve current sharing, etc., to achieve Realize the effect of true current sharing, good current sharing characteristics, and good current sharing characteristics
- Summary
- Abstract
- Description
- Claims
- Application Information
AI Technical Summary
Problems solved by technology
Method used
Image
Examples
Embodiment 1
[0031]Figure 3 is a schematic diagram of an interleaved parallel boost PFC circuit with a current sharing control module according to an embodiment of the present invention, and Figure 4 is a circuit diagram of an embodiment using DSP to realize current sharing control, which is a better one in the present invention Current sharing control circuit. The parallel boost power factor correction circuit includes a first boost circuit and a second boost circuit, and its sampling circuit includes two sampling circuits SC1 and SC2 for inductive current iL1 and iL2, which are realized by a sensor circuit; the sampling of the input voltage Vin The circuit SC3 adopts a full-wave rectification circuit (or an operational amplifier circuit, etc.); the sampling circuit SC4 of the output voltage Vbus adopts a voltage dividing resistor circuit. Four input signals (inductor current iL1, iL2, input voltage Vin, output voltage Vbus feedback voltage Vb obtained through proportional calculation) ar...
Embodiment 2
[0053] As shown in Figure 5, one difference between it and Embodiment 1 is that the difference of the inductor current is obtained by calculating the difference between the total current is and the inductor current of one of the step-up branches, specifically: sampling the first step-up The inductance current iL1 and the total current is of the circuit are used as the difference signal of the inductance current iL1 and iL2 of the first and second booster circuits through calculation (2×iL1-is) to participate in subsequent calculations, where is is equivalent to that in the first embodiment The sum of the two inductor currents (iL1+iL2), the result of the difference calculation (2×iL1-is) is equivalent to (iL1-iL2) in the first embodiment. Another difference between it and Embodiment 1 is: after the control signals Ua and Ub are sent to the comparison register, the phase shift of the control signal Ub is 180°.
[0054] Example three
[0055] As shown in Figure 6, the differenc...
Embodiment 4
[0057]As shown in FIG. 7 , the difference between it and Embodiment 1 is that the feedback current signal of the first step-up circuit is the total current signal is, and the difference of the inductor current is realized by calculating the total current and one of the inductor currents, specifically: Sampling the total current is as the current feedback signal of the first boost circuit, sampling the inductor current iL1 of the first boost circuit and calculating (2×iL1-is) as the first and second boost circuit inductor current iL1 and The difference signal of iL2 participates in subsequent operations, where is is equivalent to the sum of the two inductor currents (iL1+iL2) in Embodiment 1, and the result of the difference operation (2×iL1-is) is equivalent to (iL1 -iL2).
PUM
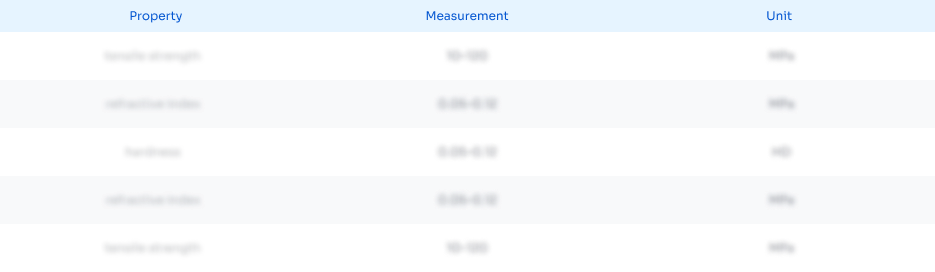
Abstract
Description
Claims
Application Information

- Generate Ideas
- Intellectual Property
- Life Sciences
- Materials
- Tech Scout
- Unparalleled Data Quality
- Higher Quality Content
- 60% Fewer Hallucinations
Browse by: Latest US Patents, China's latest patents, Technical Efficacy Thesaurus, Application Domain, Technology Topic, Popular Technical Reports.
© 2025 PatSnap. All rights reserved.Legal|Privacy policy|Modern Slavery Act Transparency Statement|Sitemap|About US| Contact US: help@patsnap.com