Elevator armored rope bending fatigue state experimental bench
A bending fatigue and wire rope technology, which is applied in the field of the bending fatigue state test bench for elevator wire ropes, can solve the problems of single function and complicated driving, and achieve the effect of flexible and convenient operation, simple and compact structure, and avoiding heavy operation.
- Summary
- Abstract
- Description
- Claims
- Application Information
AI Technical Summary
Problems solved by technology
Method used
Image
Examples
Embodiment 1
[0024] This embodiment is used for the independent bending fatigue test of steel wire ropes for elevators.
[0025]As shown in Figure 1, this embodiment includes: traction sheave 1, frequency conversion motor 2, data acquisition and control device 3, upper computer platform 4, hydraulic pump 5, hydraulic cylinder 6, tension sensor 7, tensioning wheel 8, and wire rope 9 , guide bracket 10, rope end device 11 and connection terminal 12, traction sheave 1 and tensioning sheave 8 are located at the two ends of the test bench respectively, guide bracket 10 is located between traction sheave 1 and tensioning sheave 8, and steel wire rope 9 is in turn Bypassing the traction sheave 1, the guide bracket 10 and the tensioning sheave 8, the two ends of the wire rope 9 are connected together through the rope head device 11 and the connecting terminal 12, the axle of the traction sheave 1 is connected with the output shaft of the variable frequency motor 2, and the tension The axle of the ...
Embodiment 2
[0035] This embodiment is used for the same-direction combined bending fatigue test of steel wire ropes for elevators.
[0036] As shown in Figure 3, the overall structure of this embodiment is basically the same as that of Embodiment 1, wherein: the guide bracket 10 is provided with three guide wheels 13, 14 that are in the same vertical plane, have equal diameters and have semicircular rope grooves and 15, wherein the guide wheel 13 and the guide wheel 14 have the same height and are higher than the guide wheel 15, and the wire rope 9 stretches out from the traction wheel 1 and then bypasses the guide wheel 13 and the guide wheel 14 in the same direction, and then bypasses the guide wheel in the opposite direction. Wheel 15 is wound to tension pulley 8 again, and the lower edge of guide wheel 15 is concordant with the upper edge of tension pulley 8, guarantees that the wrap angle of steel rope 9 above tension pulley 8 is 180 °. The wheel grooves of the three guide wheels are...
Embodiment 3
[0039] This embodiment is used for the reverse combined bending fatigue test of steel wire ropes for elevators.
[0040] As shown in Figure 5, the device structure of this embodiment is basically the same as the overall structure of Embodiment 1, wherein: the guide bracket 10 is provided with three guide wheels that are in the same vertical plane, have equal diameters and have semicircular rope grooves 13, 14 and 15, wherein the position of the guide wheel 14 is higher than that of the guide wheels 13 and 15. After the wire rope 9 stretches out from the traction sheave 1, it first goes around the guide wheel 13 in reverse, then goes around the guide wheel 14 in reverse, and then reverses To go around the guide wheel 15, and finally to the tension wheel 8, and its two ends are connected together by the rope head device 11 and the connecting terminal 12. The lower edge of the guide pulley 15 is flush with the upper edge of the tension pulley 8 to ensure that the wrapping angle o...
PUM
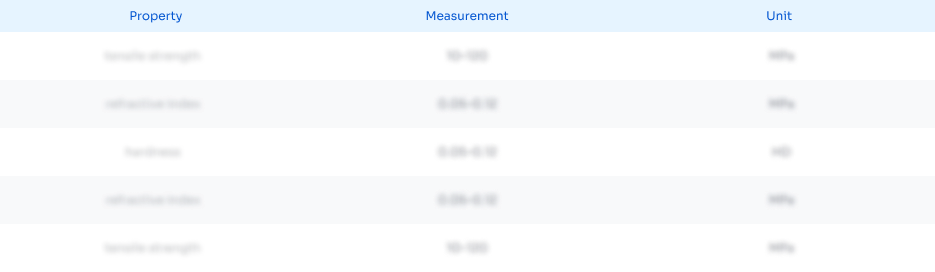
Abstract
Description
Claims
Application Information

- R&D
- Intellectual Property
- Life Sciences
- Materials
- Tech Scout
- Unparalleled Data Quality
- Higher Quality Content
- 60% Fewer Hallucinations
Browse by: Latest US Patents, China's latest patents, Technical Efficacy Thesaurus, Application Domain, Technology Topic, Popular Technical Reports.
© 2025 PatSnap. All rights reserved.Legal|Privacy policy|Modern Slavery Act Transparency Statement|Sitemap|About US| Contact US: help@patsnap.com