On-line detecting method of machine vision system for printed calico flaw
A technology of machine vision system and detection method, which is applied to the inspection of textile materials, instruments, measuring devices, etc., can solve the problems of low product pass rate, inability to guarantee the quality of inspection, and high labor intensity, so as to improve accuracy and pass The effect of reducing the detection labor intensity and ensuring the accuracy
- Summary
- Abstract
- Description
- Claims
- Application Information
AI Technical Summary
Problems solved by technology
Method used
Image
Examples
Embodiment 1
[0029] Example 1, detection of "misalignment" defects in calico images:
[0030] A. Adopt white cotton cloth, the image is as shown in Figure 1, as the detection example cloth.
[0031] B. Arrange 4 Xi'an Fangcheng 1300UM industrial cameras evenly along the horizontal direction of the calico, and fix them at a height of 1.5m. The cameras use 8mm COMPUTAR lenses, the aperture is adjusted to the maximum value, the exposure time is adjusted to 0.58ms, and the gain value (It determines the contrast effect of the image) Adjust to 0; use 2.65MHZ white light source, directly above the light, so that it is relatively insensitive to the color and pattern of the fabric, but sensitive to the light of the defect; the power supply of the display light source is a constant voltage Constant current is a stable light source without frequency variation or high frequency variation, so that clear and flawed images can be captured more stably and displayed on the computer screen.
[0032] C. The...
Embodiment 2
[0043] Example 2: Detection of "missing" defects in calico patterns:
[0044] The detection example cloth, photographing equipment and operation steps are the same as those in Example 1. Four Xi'an Fangcheng 1300UM cameras were evenly arranged horizontally along the calico and fixed at a height of 1.5m. The camera used an 8mm COMPUTAR lens, with the aperture set to 2 / 3, the exposure time set to 0.8ms, and the gain value set to 100 .
[0045] During the real-time shooting process, the dynamic automatic compensation of the light intensity of the standard image template and the correction of the pixel shift of the real-time captured image are also the same as those in Embodiment 1. The "missing" defect image of the calico pattern exceeding the precision requirements shown in Figure 3 was captured. The part within the dotted line area in Figure 3 is the missing area, and the computer screen shows that the area value of the "missing" defect in the image in Figure 3 is 20 square mi...
Embodiment 3
[0047] Example 3: Detection of "smudge" defects in calico patterns:
[0048] The detection example cloth, photographing equipment and operation steps are the same as those in Example 1. Four Xi'an Fangcheng 1300UM cameras were evenly arranged horizontally along the calico and fixed at a height of 1.5m. The camera used an 8mm COMPUTAR lens, the aperture was adjusted to 1 / 3 position, the exposure time was adjusted to 1ms, and the gain value was 50.
[0049] During the real-time shooting process, the dynamic automatic compensation of the light intensity of the standard image template and the correction of the pixel shift of the real-time captured image are also the same as those in Embodiment 1. The "smudge" defect image of the calico pattern exceeding the accuracy requirements shown in Figure 4 was obtained. The shaded part in Figure 4 is the stained area, the gray value of the image is 5, and the difference between the gray value of the image is 70, " The defect area of "smu...
PUM
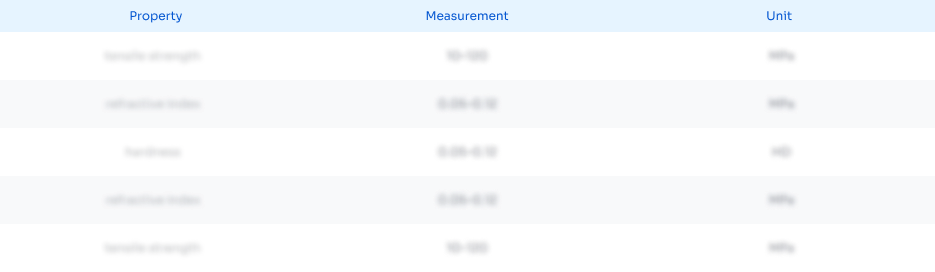
Abstract
Description
Claims
Application Information

- R&D Engineer
- R&D Manager
- IP Professional
- Industry Leading Data Capabilities
- Powerful AI technology
- Patent DNA Extraction
Browse by: Latest US Patents, China's latest patents, Technical Efficacy Thesaurus, Application Domain, Technology Topic, Popular Technical Reports.
© 2024 PatSnap. All rights reserved.Legal|Privacy policy|Modern Slavery Act Transparency Statement|Sitemap|About US| Contact US: help@patsnap.com