Correction method for position signal phase error of brushless DC motor without position sensor
A brush DC motor and signal phase technology, which is applied in the field of brushless DC motor position signal phase error correction, can solve the problems of motor operation performance impact, delay calculation of phase error, etc., and achieve good real-time performance and simple effect
- Summary
- Abstract
- Description
- Claims
- Application Information
AI Technical Summary
Problems solved by technology
Method used
Image
Examples
Embodiment Construction
[0017] When the H_pwm-L_on modulation method (see Figure 3) is used, there is a freewheeling current in the non-conducting part of the brushless DC motor corresponding to the counter electromotive force less than zero. Let the freewheeling part in the 60° non-conduction working interval after the negative 120° conduction interval of the motor phase winding be M 1 In the working interval, the freewheeling part in the 60° non-conducting working interval after the forward 120° conduction interval of the phase winding is M 2 working area.
[0018] Let M 1 The average value of freewheeling current in the interval is I m1 ,M 2 The average value of freewheeling current in the interval is I m2 , Δi=I m2 -I m1 . I m1 , I m2 Has the following relationship: when the motor commutates accurately, I m1 =I m2 , Δi=0 (see Figure 4); when commutating ahead, I m1 > I m2 , Δim1 m2 , Δi>0, Δi increases as the lag commutation angle increases (see Figure 6). According to this characte...
PUM
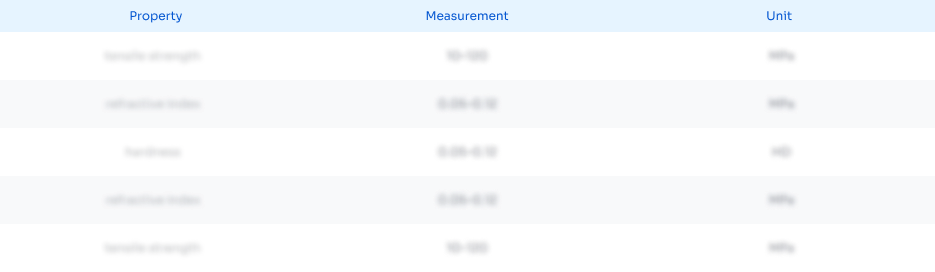
Abstract
Description
Claims
Application Information

- R&D
- Intellectual Property
- Life Sciences
- Materials
- Tech Scout
- Unparalleled Data Quality
- Higher Quality Content
- 60% Fewer Hallucinations
Browse by: Latest US Patents, China's latest patents, Technical Efficacy Thesaurus, Application Domain, Technology Topic, Popular Technical Reports.
© 2025 PatSnap. All rights reserved.Legal|Privacy policy|Modern Slavery Act Transparency Statement|Sitemap|About US| Contact US: help@patsnap.com