Minisize transformer device and manufacturing method therefor
A technology of a micro-transformer and a manufacturing method, which is applied to the manufacture of inductors/transformers/magnets, transformers/inductor cores, electrical components, etc., can solve the problems of inconvenient assembly, high defect rate, complex production process, etc., and achieve simplification Process, the effect of reducing production and assembly costs
- Summary
- Abstract
- Description
- Claims
- Application Information
AI Technical Summary
Problems solved by technology
Method used
Image
Examples
Embodiment Construction
[0015] A microtransformer and its manufacturing method according to a preferred embodiment of the present invention will be described below with reference to related drawings.
[0016] With reference to Fig. 3, Fig. 4, Fig. 5, Fig. 6, Fig. 7, a kind of miniature transformer of preferred embodiment of the present invention is provided with transformer reel 1, transformer iron core 2. Wherein, the transformer iron core 2 is made of elongated magnetic material, the two ends of the transformer reel 1 have flanges 101, 102, the flanges 101, 102 cover the two short ends 105, 106 of the transformer iron core 2, and the flanges The parts 101 and 102 are connected as a whole by two extension parts 103 and 104, the extension parts 103 and 104 cover the two long ends 107 and 108 of the transformer core 2, and the transformer reel 1 is directly molded and tightly covered by a single mold 6 Transformer iron core 2 surroundings.
[0017] The manufacturing method of a kind of miniature tran...
PUM
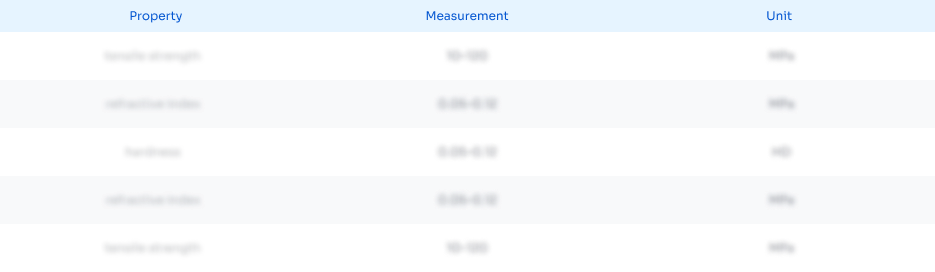
Abstract
Description
Claims
Application Information

- R&D
- Intellectual Property
- Life Sciences
- Materials
- Tech Scout
- Unparalleled Data Quality
- Higher Quality Content
- 60% Fewer Hallucinations
Browse by: Latest US Patents, China's latest patents, Technical Efficacy Thesaurus, Application Domain, Technology Topic, Popular Technical Reports.
© 2025 PatSnap. All rights reserved.Legal|Privacy policy|Modern Slavery Act Transparency Statement|Sitemap|About US| Contact US: help@patsnap.com