Method for planning smooth and non-interference tool route of 5-axis numerical control machining
A tool path, non-interference technology, applied in the direction of digital control, electrical program control, etc., can solve the problems of limiting tool flexibility, increasing algorithm complexity, and not being able to correctly analyze the manufacturability of workpieces, so as to reduce time and avoid repetition Adjustment, computationally efficient effects
- Summary
- Abstract
- Description
- Claims
- Application Information
AI Technical Summary
Problems solved by technology
Method used
Image
Examples
Embodiment Construction
[0044] The technical solution of the present invention will be described in further detail below in conjunction with the accompanying drawings and embodiments. The following examples are not intended to limit the present invention.
[0045] The flow chart of the planning method for the smooth and non-interfering tool path of five-axis CNC machining proposed by the present invention is shown in Figure 1. Firstly, the geometric model of the tool, workpiece and obstacles is established. Interfering objects; use the section method or equal parameter method to calculate the contact point between the tool and the workpiece to obtain the tool contact sequence, and determine the position of the tool point according to the tool contact sequence and tool shape; uniform discretization to uniformly triangulate the Gaussian sphere , take the vertices of the triangular mesh to determine the discrete reference direction of the tool axis; detect the accessibility of all tool contacts in the d...
PUM
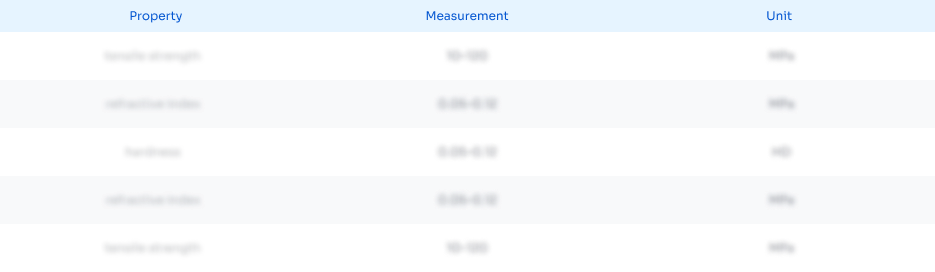
Abstract
Description
Claims
Application Information

- R&D Engineer
- R&D Manager
- IP Professional
- Industry Leading Data Capabilities
- Powerful AI technology
- Patent DNA Extraction
Browse by: Latest US Patents, China's latest patents, Technical Efficacy Thesaurus, Application Domain, Technology Topic, Popular Technical Reports.
© 2024 PatSnap. All rights reserved.Legal|Privacy policy|Modern Slavery Act Transparency Statement|Sitemap|About US| Contact US: help@patsnap.com