Manufacturing technique method of sheet material covering film and laminating machine thereof
A production process and a laminating machine technology, which are applied in the field of floor lamination production process methods and lamination devices, can solve the problems of waste of membrane material, low efficiency of production mode, low quality of lamination and film cutting, etc., so as to improve production efficiency , Guarantee the effect of product quality
- Summary
- Abstract
- Description
- Claims
- Application Information
AI Technical Summary
Problems solved by technology
Method used
Image
Examples
Embodiment Construction
[0032] Production process of the present invention is as follows:
[0033] Step A): The board slides forward on the conveying roller table. When the front end of the board reaches the first detection position, the board feeding driving device accelerates to drive the board to accelerate forward. The film coating device drives the board film and the board to advance synchronously. on the plate;
[0034] Step B): When the tail end of the board reaches the second detection position, the board feeding driving device starts to decelerate, so that the forward speed of the board gradually decreases;
[0035] Step C): The first detection position is located at a certain distance behind the second detection position. When the tail end of the plate reaches the first detection position, the plate feeding driving device stops and brakes to position the plate;
[0036] Step D is as follows: use a separation device to separate the distance between two adjacent boards after film coating to ...
PUM
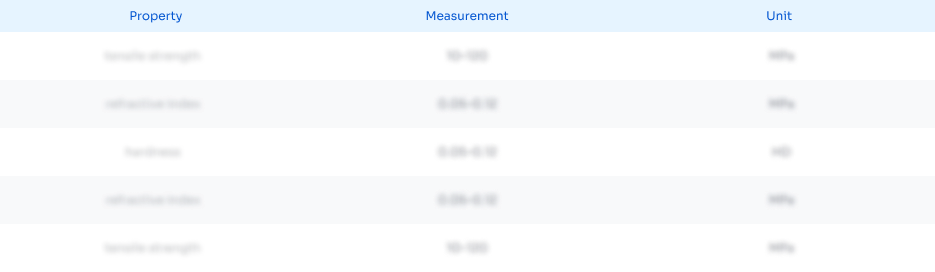
Abstract
Description
Claims
Application Information

- R&D
- Intellectual Property
- Life Sciences
- Materials
- Tech Scout
- Unparalleled Data Quality
- Higher Quality Content
- 60% Fewer Hallucinations
Browse by: Latest US Patents, China's latest patents, Technical Efficacy Thesaurus, Application Domain, Technology Topic, Popular Technical Reports.
© 2025 PatSnap. All rights reserved.Legal|Privacy policy|Modern Slavery Act Transparency Statement|Sitemap|About US| Contact US: help@patsnap.com