Workpieces reference frame marking method based on relative measurement
A technology of workpiece coordinates and relative measurement, which is applied to measuring devices, instruments, etc., can solve problems such as inaccurate calibration, calibration errors of measurement systems, robot system errors, etc., and achieve the effects of accurate results, improved operation accuracy, and simple operation process
- Summary
- Abstract
- Description
- Claims
- Application Information
AI Technical Summary
Problems solved by technology
Method used
Image
Examples
Embodiment Construction
[0032] The core idea of the present invention is: calibrate the initial value of the workpiece coordinate system pose (Wobj), and use the transformation matrix between the initial value of Wobj and the actual value to complete the calibration of the workpiece coordinate system.
[0033] Referring to Fig. 1, it is a structural diagram of an embodiment of the present invention;
[0034] As shown in the figure, it includes a robot 10 , a measuring device 11 , and a workpiece 12 , wherein the base 101 of the robot 10 and the measuring device 11 are respectively fixed, for example, in the world coordinate system, and the workpiece 12 is fixed at the end 102 of the robot 10 .
[0035] The measuring device 11 may be a linear displacement sensor (LVDT) or a point laser measuring device.
[0036] Referring to Fig. 2, it is a flowchart of an embodiment of the present invention;
[0037] Step 201, calibrate the positional relationship between the relative zero point of the measuring d...
PUM
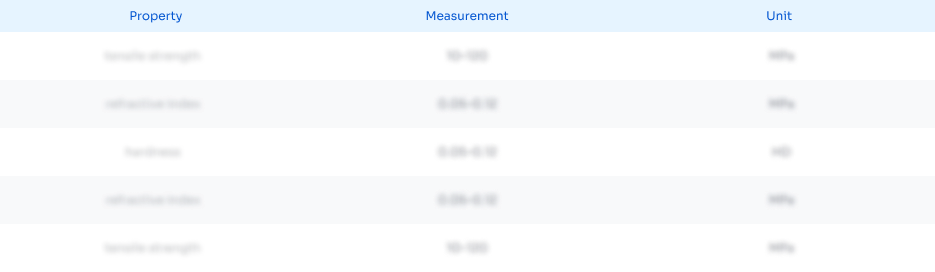
Abstract
Description
Claims
Application Information

- Generate Ideas
- Intellectual Property
- Life Sciences
- Materials
- Tech Scout
- Unparalleled Data Quality
- Higher Quality Content
- 60% Fewer Hallucinations
Browse by: Latest US Patents, China's latest patents, Technical Efficacy Thesaurus, Application Domain, Technology Topic, Popular Technical Reports.
© 2025 PatSnap. All rights reserved.Legal|Privacy policy|Modern Slavery Act Transparency Statement|Sitemap|About US| Contact US: help@patsnap.com